当下,碳达峰、碳中和已经成为全球的共识,国家也明确提出“2030年前实现碳达峰、2060年前实现碳中和”的发展目标。在这一长期目标的推动下,为尽早实现节能减排,除了发展和探索新能源,推出更高效、更环保、又兼顾动力的节能发动机产品仍然是各大汽车厂商尝试突破的技术领域。2018年,日产推出全球首款量产VC-Turbo超变擎,做到了发动机动力性能和燃油经济性能的平衡,而其制造国产化,也为中国市场带来更具竞争力的价格。
“我们的2.0T机型产品有两种,一种是4缸直列可变压缩比涡轮增压发动机,一种是3缸直列可变压缩比涡轮增压发动机。为了兼顾经济性,我们选择两种型号发动机共线生产的方式,因此对生产线提出了更高要求,不仅要实现自动化加工,还需要具备合理的柔性化。”东风日产发动机技术负责人陈小森介绍道。
东风日产发动机技术负责人陈小森s
挑战
2019年1月,东风日产委托柯马设计实施一个高速自动化的发动机总成装配系统,包括了缸盖装配线、短发装配线、活塞连杆装配线、发动机裸机装配线以及发动机总成装配线等主要线体,及缸盖精加工设备、机器人上下料工位、随行托盘等非标准机加工作站位。柯马提供包括工艺方案、刀具、夹具、自动化方案从设计到制造到全生命周期服务。
日产VC-Turbo超变擎是世界首款机械层面的量产可变压缩比发动机,而其智能机加及装配生产线制造项目则是国内唯一一条集成了缸盖金属切削,及发动机装配的智能自动生产线。项目的挑战在于实施过程中,市场上没有可供参考的工艺,在其设计、实施期间,凭借柯马对自动化技术的创新能力及客户对产品的高品质要求,不断探索多种新型节能发动机制造关键制造工艺。
同时,为了满足客户年产40万台的高产能目标,本项目需要用工业化的效率和手段生产个性化产品,实现全球范围内的可变工况发动机智能机加及装配生产线个性化定制的商业模式。
解决方案
生产线融合了多种先进发动机自动化装配技术。比如,七轴机器人技术运用到缸盖的自动上料工位,实现了大范围抓取工件;采用六轴机器人自动上螺栓,可以实现多角度变位,达到自动、灵活拧紧等。整线有超过60个自动工位应用了广泛的自动化和机器人技术,从关键装配工艺技术角度,项目还实现了以下技术创新:
柯马专利的 SmartCell 柔性装配中心技术。该技术整合了装配自动化和加工中心技术,通过多轴数控与类加工中心换刀的快速更换工具技术,实现了缸盖一站式装配。发动机装配线管理着各种复杂的装配过程,包括由于高度自动化困难,传统上通过手工传统上由人工实现的装配任务的升级。
创新柔性压装方式以及视觉定位系统实现自动上料的无序抓取。为提高生产效率,满足机器人的前端来料定位更高的柔性化要求,快速、准确识别无序来料的状况,柯马通过使用机器人视觉定位系统,识别料框中工件位置并随机无序抓取到接料台上,为量产进行自动上料。未来无论是新增机型或者产品变更,只需要更新程序即可实现兼容,无需停线和再投资。这样一来,不仅后续省去维护成本,并能将设备的故障率无限降低至接近于零,大大降低了后期的使用成本和减轻了设备维修人员的工作负荷。同时产线辅以电缸移动、压头快换和工件移动的方式,可灵活实现任意位置任意零件的柔性压装。
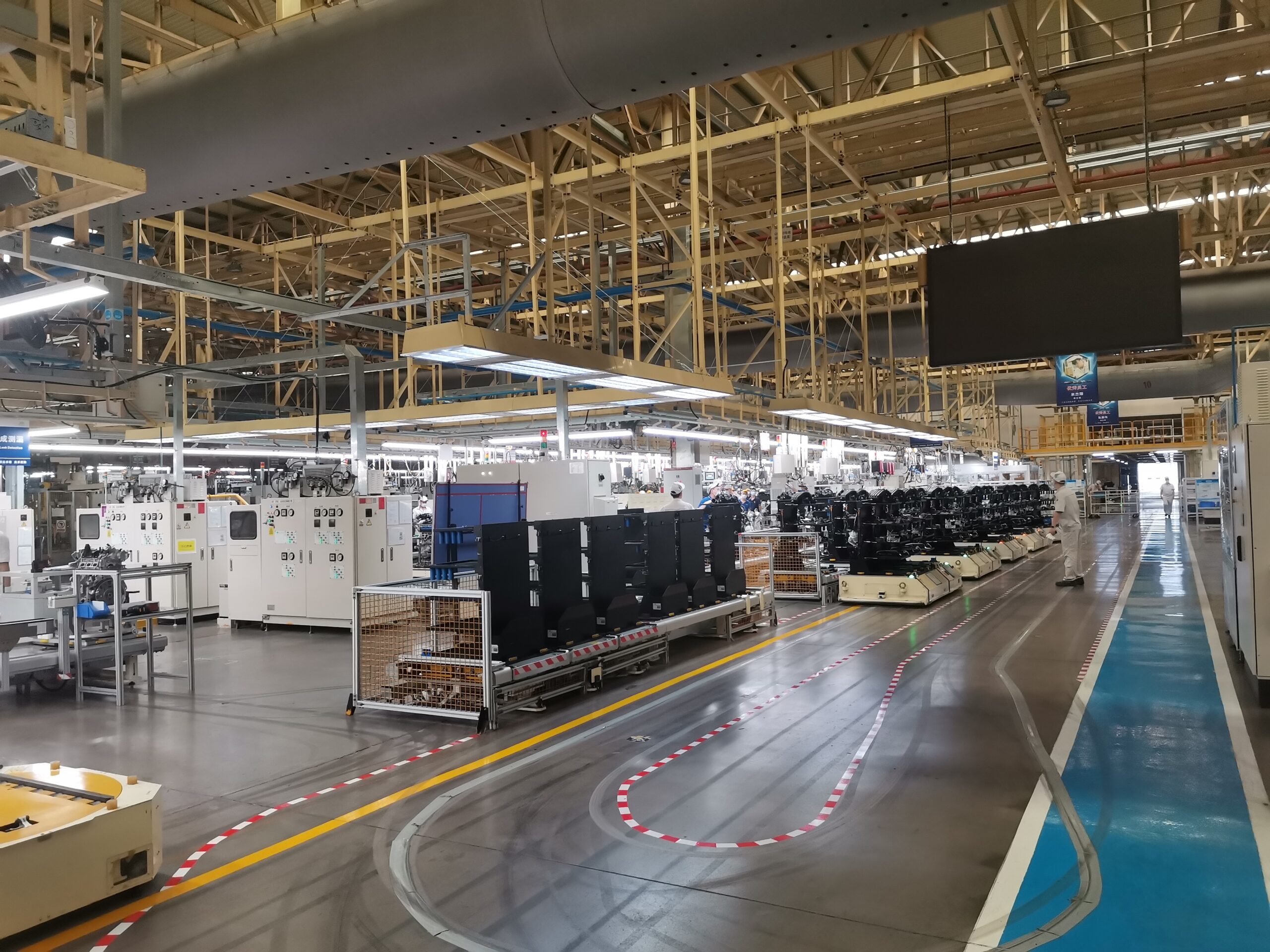
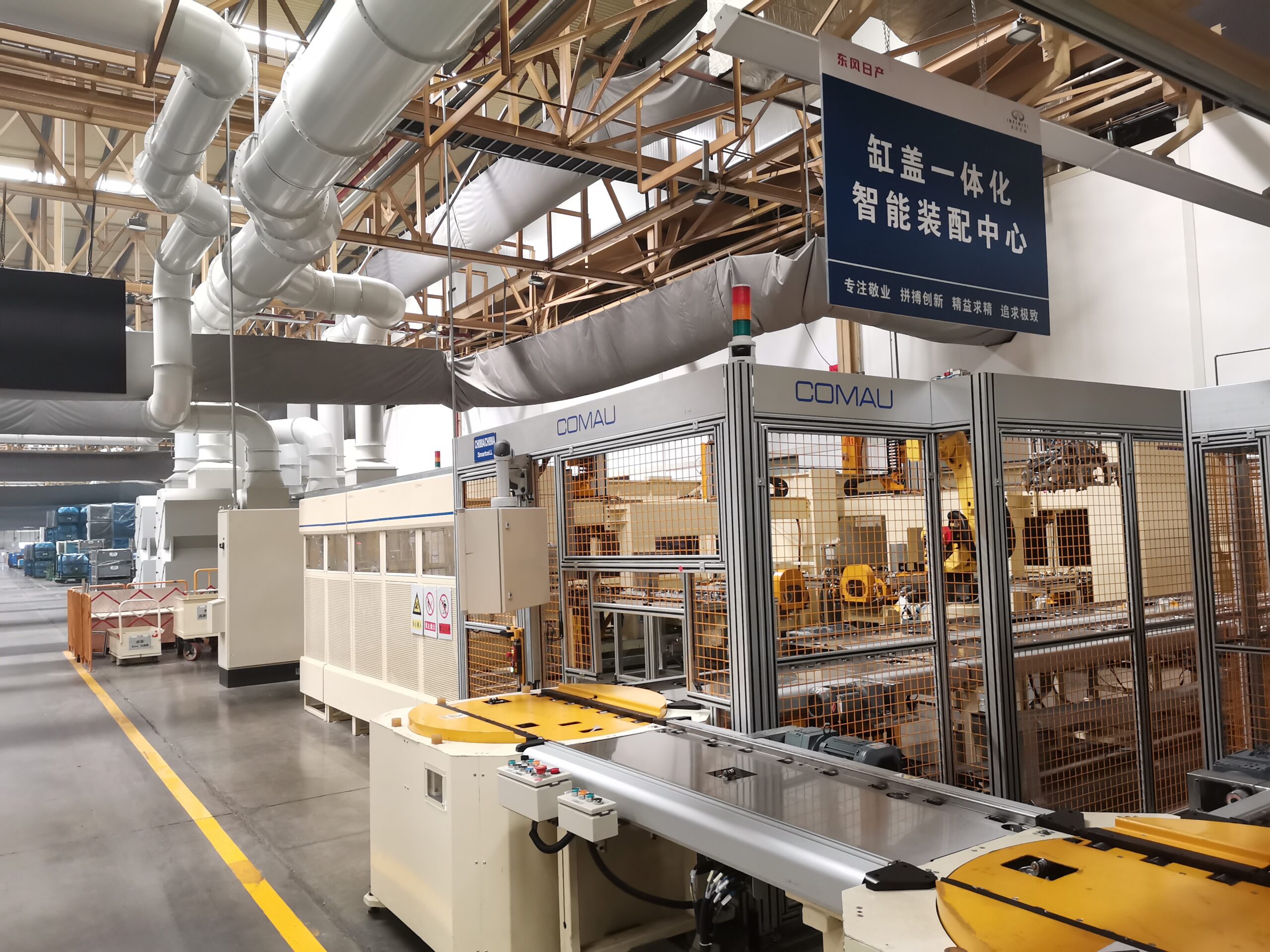
成果
本项目实施过程中应用多种先进技术,解决了新型节能发动机制造关键问题。同时,项目设计过程中,通过使用产品生命周期管理软件,打通了从设计到制造的数字化通道,达成了对设计、生产制造过程的全过程数字化,实现了流程透明,有效控制设计质量、减少设计风险、降低制造成本、缩短生产周期,成为后续数字化制造重要的数据来源。
柯马解决方案真正实现了全柔性的生产,若需新增或改造设备,只用更改设备的程序和柔性快换工具即可实现多品种混线生产,同时大幅度提高了发动机制造的自动化率。两种机型在2020年8月均顺利进入量产阶段,年产能达40万。
东风日产发动机管理负责人白忠金表示,“柯马团队证明了他们具备完整自动化装配和机加工方面的独特能力。他们拥有我们所需的技术体系和强大经验,使这个项目在预算和进度方面都能保持竞争力。”
k
每年的产能
两台发动机 设计用于同地生产
+
0%
单一装载机成功率提高