开发先进技术和制造工艺
柯马在开发先进技术和汽车行业制造工艺上取得的卓越成效,使其在巴西新款菲亚特Pulse和Fastback开发中发挥了关键作用。Pulse是菲亚特在巴西推出的首款SUV车型,而FASTBACK则是其推出的首台SUV轿跑车,是菲亚特2022年在本地市场推出的主打产品之一。
柯马的任务是开发一条能够同时生产这两款SUV车型的高产自动化生产线,专门用于车身主线、侧围和补焊活动。为此,在巴西米纳斯吉拉斯州贝廷市斯特兰蒂斯迪斯汽车厂进行的全面改造项目中,柯马为其部署了先进的车身装配解决方案。
“除了应对固有的自动化挑战之外,柯马团队迅速提出并整合了不同的关键技术,以达到我们的质量和生产周期时间目标。”斯特兰蒂斯南美生产副总裁Glauber Fullana表示。“该项目是我们工业4.0战略的一部分,赋予了我们更大的灵活性,让我们可以在同一条生产线上生产不同版本和其他型号。”
挑战
斯特兰蒂斯给柯马提出的挑战是为其设计一种尖端的解决方案,使该公司能够使用现有平台来灵活的生产两种不同SUV车型,应对其独特尺寸和规格变化,以达到公司既定的生产目标、质量目标和周期时间。
此外,柯马需要改造和翻新主线和补焊线,以确保大规模、经济高效地生产多种车型,同时保证与汽车及乘用车共享这些生产线,保持它们的生产连续性。此外,由于安全和灵活性是该项目的两大主要支柱,因此需要尽量减少在装配线上的生产线干预,同时优化自动化效率。
最后,除了管理复杂的项及其技术复杂性外,柯马团队还得面临新冠疫情导致的项目停止问题,不得不停工六个月。
解决方案
凭借几十年来以来的丰富客户经验及其所积累的一系列坚实的技能,柯马充分利用其当地支持和在各种工程领域的技术专长来满足该项目的严格要求。第一步是与汽车制造商直接合作,持续改造和翻新总共74个自动和10个手动工位,用于生产SUV主线、侧围和补焊活动。
具体而言,工程团队整合了柯马的高速工业机器人、先进的视觉系统、3D粘接剂点胶、数字应用和交钥匙设备,以创建 3 个主要工作站:主线制造系统(32个自动和2个手动工位)、另加28个自动工位以及6条用于车身侧围装配线的手动装载线、以及补焊装配线(14个自动和2个手动工位)。该综合制造解决方案还配备了柯马的OpenGate系统,以确保几何精度,同时赋予其灵活处理多种车型配置的能力以及卓越的52秒的平均周期时间。
为了优化这些复杂生产线的设计和改造,柯马采用虚拟调试能力和工艺模拟技术,使团队能够在现场调试之前测试预期的性能和功能。这样,团队能够预测机器人序列中以及机器人和PLC控制器之间的通信可能产生的问题。柯马和斯特兰蒂斯集团工程师在虚拟环境中创建了工厂总视图,由此可以识别改进点,增强过程监控,并更好地利用工厂已有设备,并优化各个工位和各条生产线之间的内部流通。所有这些特点的结合对于有效实现限额成本设计的方法至关重要。
另一个重要亮点是使用IO-Link技术监测供水和压缩空气供给系统,确保实时数据分析和并敏捷的检测可能存在的问题。同时它集成了PLC软件以优化维护活动,并可通过企业网络执行机器人备份活动,提高整条生产线的长期可靠性。
成果
柯马和斯特兰蒂斯共同合作之后,重塑的的生产线使斯特兰蒂斯能够批量装配新款Pulse SUV的5种不同版本,其中包括Pulse Abarth车型和Fastback SUV的2种不同版本,与此同时能够装配其它菲亚特车型。
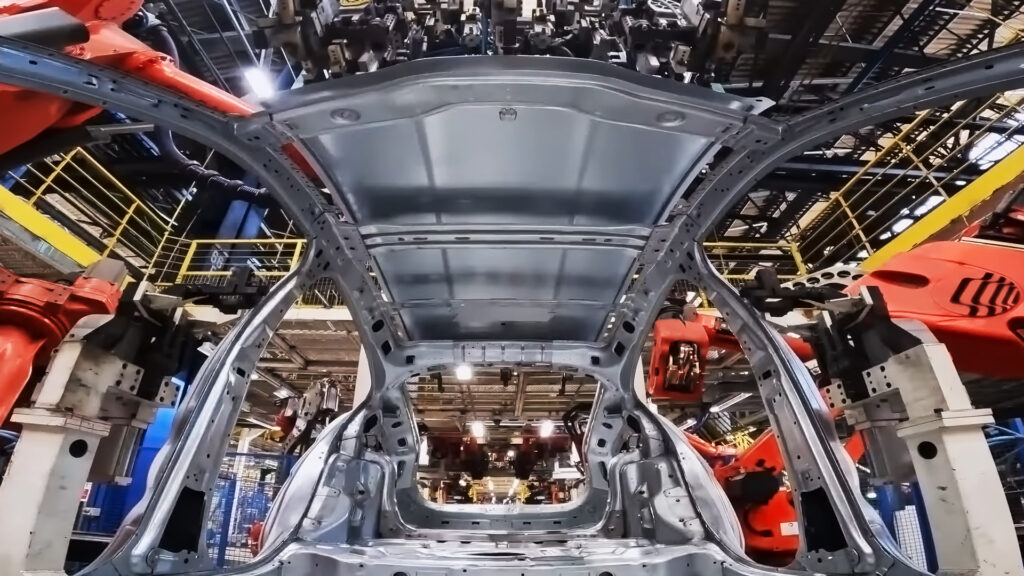
为了满足可持续性目标,柯马尽量可能的利用原有的平台,在此基础上新增了17台机器人和45 把新焊枪,用于处理SUV车身和侧围的1000个焊点。该解决方案还最大限度地减少了工具更换和生产线干预,节省了时间,并对项目的整体可持续性产生了积极影响。
柯马深厚的工艺知识以及与客户工程团队的全面整合,使其能够高效地按时交付项目。该团队于2019年10月签署了预期交付里程碑,之后由于全球新冠疫情被迫停工6个月。然而,由于Pulse和Fastback将与其它菲亚特车型分享共同的生产线,所以无法更改原始项目启动日期。柯马的创造力、对工作的倾注以及对虚拟调试和工艺模拟的运用,让该团队在项目意外停止的情况下仍然能够优化现场交付目标。
该创新解决方案由巴西柯马开发,受到了罗马尼亚柯马公司的工程支持,其先进的视觉系统技术确保了所需的美学几何精度和斯特兰蒂斯集团所要求的焊接精度。此外,该解决方案还为客户提供了更高的设备效率,并可根据需要灵活地从批次生产转向随机混合生产。事实上,该项目证明了柯马始终致力于提供先进的制造解决方案,为巴西汽车工业开发优质车辆献计出力。
三条主要生产线上的自动工作站
三条主要生产线上的手动工作站
用于处理SUV车身和侧围的个焊点