吉普公司在巴西伯南布哥最现代化的汽车制造厂之一为全新SUV车型生产做准备时,提出的条件非常清楚与直接。柯马将负责扩展车体生产线,让汽车制造商能够采用柔性生产方式,任意混合生产已有3款车型以及吉普7座指挥官,确保仍然保存平均每小时48辆汽车的生产率与生产线的可扩展性。为了提高产能,柯马在戈亚尼亚吉普汽车厂已有620台装配与焊接机器人的基础上,添加了24台新机器人、24把焊钳、4条输送带。另外,柯马改进了14条生产线上,使其集自动、半自动与手动操作为一体。这些改动在工厂自然停产期间进行,确保尽量降低对生产的影响。
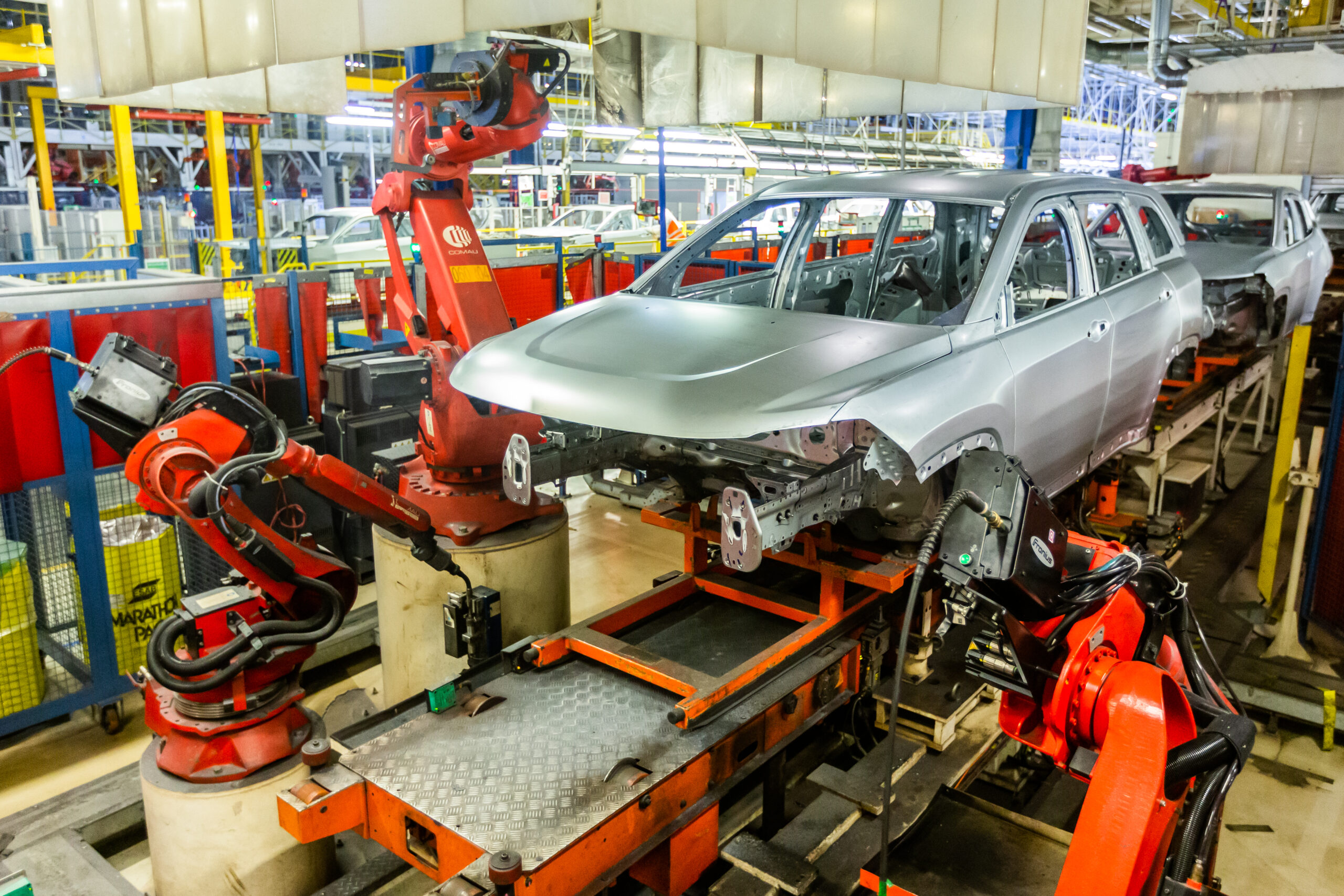

吉普工厂经理Mateus Marchioro说:“从项目开始,柯马就展示了其精湛的技术能力、在自动化方面的专业以及对成功的承诺。尽管工厂由于新冠大流行而停产2个月,但是团队还是提早完成了项目的所有阶段。最重要的是,所提出的解决方案比我们预期所需的辅助设备与手动工艺操作更少。我们对新生产线的总体性能非常满意。”
吉普工厂经理Mateus Marchioro说
挑战
吉普给柯马带来的挑战是设计一个创新的解决方案,让其能够在巴西已生产其它3款最畅销车型的生产线上生产最新的SUV,同时不影响生产或周期节拍。另一个挑战是提高自动化水平与工艺效率。因为从生产一个车型转换到另一车型需要更换工装,如果没有预先精心设计,可能导致效率低下。最后,这些生产线将需要足够的内在柔性让吉普将来可以引进新车型。
柯马精湛的技术及其与吉普工程团队的全面融合,确保了制造商项目的良好实施与按时完成。仔细了解真正的生产周期之后,柯马工程师们使用模拟工具全面了解与模拟装配生产线部署所要进行的所有修改,然后才付诸实际。他们对所有设备与资源的位置及使用进行了精确的诊断,确保所有的修改都会在数字化演示情景中显示标出。这样工作团队可以优化工厂调试,将由修改引起的停机时间减少到最低限度。柯马团队也使用虚拟调试安排工艺模拟,以加速各条生产线的实施。
解决方案
为了满足吉普车型柔性生产要求,柯马工程师将创新的生产系统由生产3款车型扩展到了4款车型,并可任意混合生产这些车型。这是该系统首次可以生产4款不同的车型,其设计预留新设备安装空间,以便引入其它新车型。在生产线的某处,14台机器人在52秒内同时焊接100个定位焊点,仅一个操作就能完成车体与底盘合身,同时确保车身的完美形状。在另一阶段,70台机器人同时涂抹结构粘胶剂,以加强车体刚度以及防尘防水能力。每辆汽车在装配过程中共接受3000个定点焊接。
生产线的其它修改包括完善柯马VersaRoll自动焊接与装配系统。因此,工程团队无需对设备进行校准,同时又优化了每个工作站的机器人数量。同样的,工具托盘穿梭车也得以扩展,有史以来第一次对4个工作站进行操作,因此更适应新SUV的特定装配需求。
为了应对新冠疫情带来的挑战,例如工厂强制封闭期间无法进入工厂,巴西的柯马采用了灵活的项目管理方法。团队采用远程办公的智能方式,在工厂逐步安全恢复生产之前对各个单元与虚拟调试工具进行模拟。团队也很好的管理了零部件未在期限内收到的问题,并且将重点放在供应及时的项目部分。因此,柯马能够推动项目发展,从头到尾只需不到24个月就能部署598项目。最重要的是,这样做没有影响吉普戈亚尼亚工厂的生产流与产量。
成果
柯马采用精益管理的制造方法,其创新解决方案具有高度自动化流程,于此同时能减少对辅助机械设备的需求。该方案不再使用传感器或电眼通过形状探测零部件,而是使用摄像头。生产线工作站实施全线数字化3D设计,确保机器人操作时完全对准。同时应用柯马专有解决方案,例如激光焊接、视觉系统以及RHEvo滚边解决方案。另外,其配置兼容工业4.0,采用了IO-link科技监控关键工艺,例如水与压缩空气系统,迅速有效的帮助探测任何问题。所有的这一切帮助吉普提高设备效率,完善质检资源。
为了保护客户投资的可扩增能力,整个项目的设计旨在方便吉普未来引进生产新车型。另外,该项目由巴西领导,并获得了罗马尼亚柯马、意大利柯马与中国柯马的支持,展现了柯马应对最严格生产标准挑战的能力。由此也促进巴西柯马扩展本地网络,增长自动化、数字化与智能科技方面的长足专业经验,为吉普提供生产高端汽车所需的速度、质量与效率。
共有14条综合生产线可任意装配
+
台柯马机器人
每52秒焊接 个定位焊点
扩展过程中生产率损失为