Atualmente, a redução e neutralidade de emissões de carbono se tornaram compromissos globais, com a China indicando claramente seu objetivo de “atingir um pico de emissões até 2030 e a neutralidade de carbono até 2060″. Impulsionados por esse objetivo de longo prazo, os principais fabricantes de automóveis estão focados em conseguir eficiência energética e reduzir as emissões o quanto antes, assim como pesquisar e desenvolver novas fontes de energia e criar produtos mais eficientes, ecológicos e com melhor desempenho energético. Em 2018, por exemplo, a Nissan lançou o primeiro motor VC-Turbo produzido em massa no mundo – um motor de compressão variável que equilibra a relação entre potência e consumo de combustível. A montadora de automóveis também conseguiu oferecer um preço mais competitivo no mercado chinês, regionalizando a produção.
“Nosso modelo 2.0T, possui um motor de 4 cilindros em linha com compressão variável e um motor de 3 cilindros em linha com compressão variável e turbo carga”, explicou o líder técnico da Dongfeng Nissan Engine, Chen Xiaosen. “Por razões estratégicas, decidimos produzir os dois tipos de motores em uma única linha. No entanto, o método de produção colinear eleva os padrões de produção, tanto para realizar o processamento automático como também para assegurar um grau razoável de flexibilidade.”
Chen Xiaosen, líder técnico da Dongfeng Nissan Engine
Desafio
Em janeiro de 2019, a Dongfeng Nissan contratou a Comau para projetar e implementar um sistema automatizado de montagem de motores de alta velocidade, que incluiria as linhas principais (conjunto de cabeçote de cilindro, montagem dos componentes do bloco do motor, montagem de pistões e bielas, e a montagem do motor), estações de usinagem não padronizadas, como equipamentos para o acabamento do cabeçote do cilindro, estações de carga e descarga robotizadas e bandejas de acompanhamento.
O Nissan VC-Turbo, sendo o primeiro motor de compressão variável produzido em massa no mundo a um nível mecânico, seria o único na China com um projeto inteligente de fabricação, usinagem e montagem capaz de integrar corte de metais do cabeçote do cilindro a montagem do motor em uma linha de produção automatizada. E por isso, a Comau não conseguiria utilizar processos padronizados.
Para enfrentar esse desafio, uma série de processos-chave para a produção do novo motor energeticamente eficiente foram explorados durante as etapas de criação e a implementação da linha, com a tecnologia e inovação da Comau em automação. O design de processos também precisaria levar em consideração o alto grau de exigência em qualidade do cliente para seus produtos.
O desafio adicional seria alcançar a meta de produção desafiadora do cliente, de 400.000 unidades por ano. Para isso, a Comau precisaria utilizar simultaneamente, eficiência na industrialização e aproveitar o máximo de recursos para produzir produtos personalizados em um modelo de negócios embasado em usinagem inteligente e, considerando também, as condições de trabalho variáveis e a montagem de estações em linha para uma produção em escala global.
Solução
Para atender às exigências de qualidade, produtividade e eficiência do cliente, a Comau projetou uma linha de produção inovadora, que reúne uma variedade de tecnologias avançadas de automação à montagem de motores. Isso inclui, o uso de robôs de sete eixos para a estação de carregamento automático da linha do cabeçote, capazes de trabalhar com uma ampla variedade de peças, o uso de robôs de seis eixos para aparafusamento automático, que permite o posicionamento em vários ângulos para obter um aperto automático. Com mais de 60 estações automatizadas ao longo de toda a linha, a gama de tecnologias de automação e robótica é muito ampla e permitiu à Comau aplicar várias de suas soluções exclusivas como parte dos principais processos de montagem.
A tecnologia patenteada da Comau – SmartCell (Centro de Montagem Flexível) – é uma dessas inovações. Integrando tecnologia de automação, montagem e usinagem em um único centro de montagem, seu CNC (Controle Numérico de Computador) multi eixos e a tecnologia de troca rápida de ferramentas permitem a montagem do conjunto do cabeçote numa só parada. Isso permite que a linha de montagem do motor consiga lidar dinamicamente com uma variedade de processos de montagem complexos, incluindo a melhoria de tarefas de montagem que são tradicionalmente realizadas por trabalho manual devido ao alto grau de dificuldade de sua automação.
O centro de montagem flexível SmartCell utiliza robôs de coordenadas retangulares (ligação de 6 eixos) para automatizar a montagem completa das peças do cabeçote do motor, incluindo válvulas do cabeçote, vedações de óleo de válvula, molas de válvula, placas de travamento de válvula e assentos superiores. Isso foi possível com a organização de vários conjuntos de dispositivos de montagem de troca rápida automática e do uso de processos de montagem paralelos, trabalhando com robôs de 6 eixos para executar a carga e descarga automatizada dos cabeçotes de cilindro e paletes.
Além disso, foi implementado um método inovador de ajuste por pressão e um sistema de visão que permite o carregamento automático e a coleta aleatória de peças. A Comau utiliza o sistema de posicionamento visual do robô para detectar a posição da peça de trabalho e coletar aleatoriamente na mesa de alimentação para a produção em massa. Isso garante maior eficiência de produção, maior flexibilidade em termos de posicionamento do material na frente do robô e detecção mais rápida e precisa do material de entrada em condições aleatórias. No futuro, quando ocorrer uma alteração de modelo ou de produto, o cliente, simplesmente, poderá atualizar o programa em vez de desligar o sistema ou reinvestir em novas tecnologias. Desta forma, os custos de manutenção são otimizados. Mais importante ainda, a taxa de falha da linha pode ser diminuída a praticamente zero, o que reduz muito o custo de uso da linha e a carga de trabalho do pessoal de manutenção. A linha de produção também é complementada pelo movimento do cilindro elétrico, que pode realizar dinamicamente o aperto de qualquer peça, em qualquer posição.
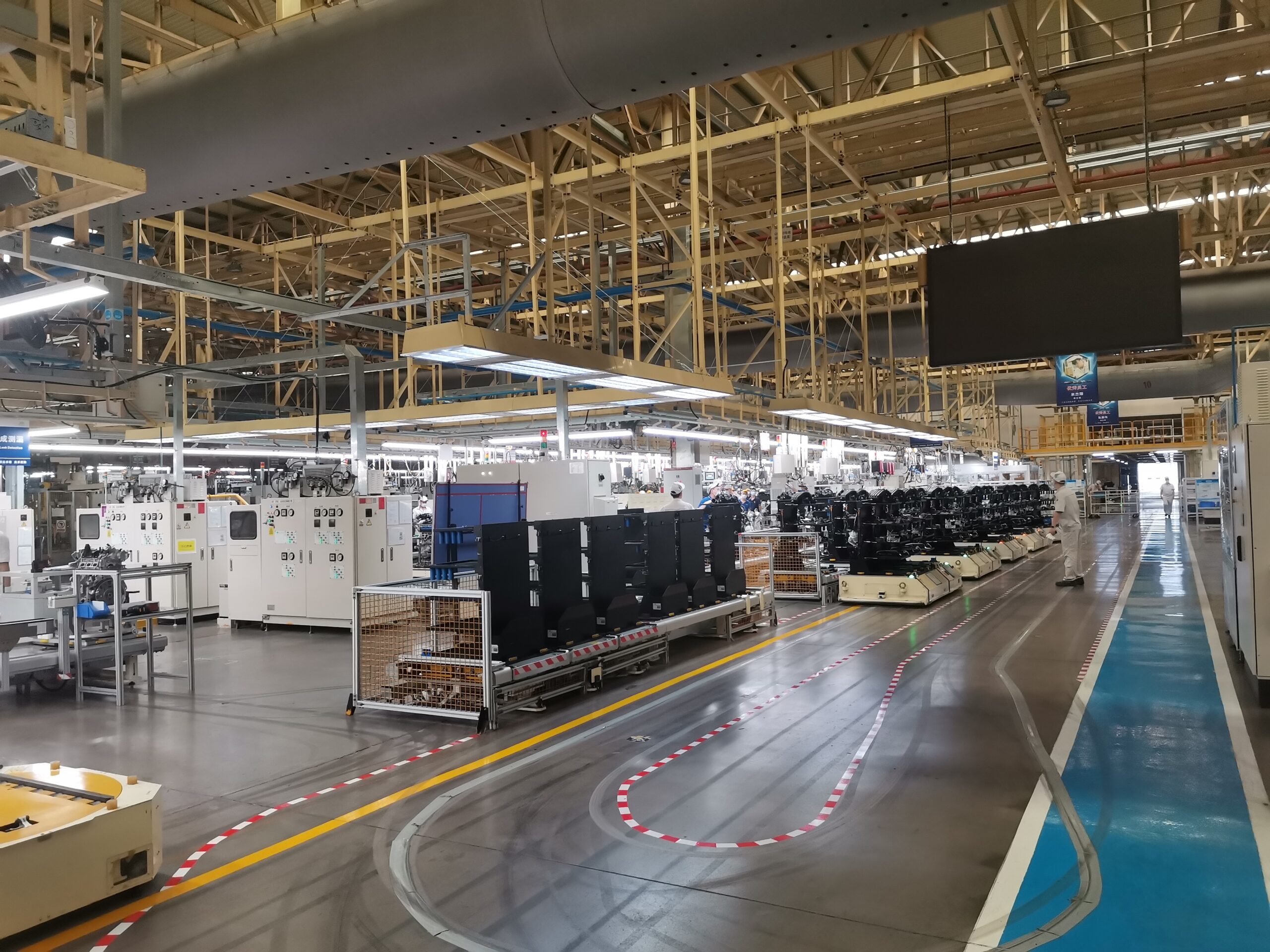
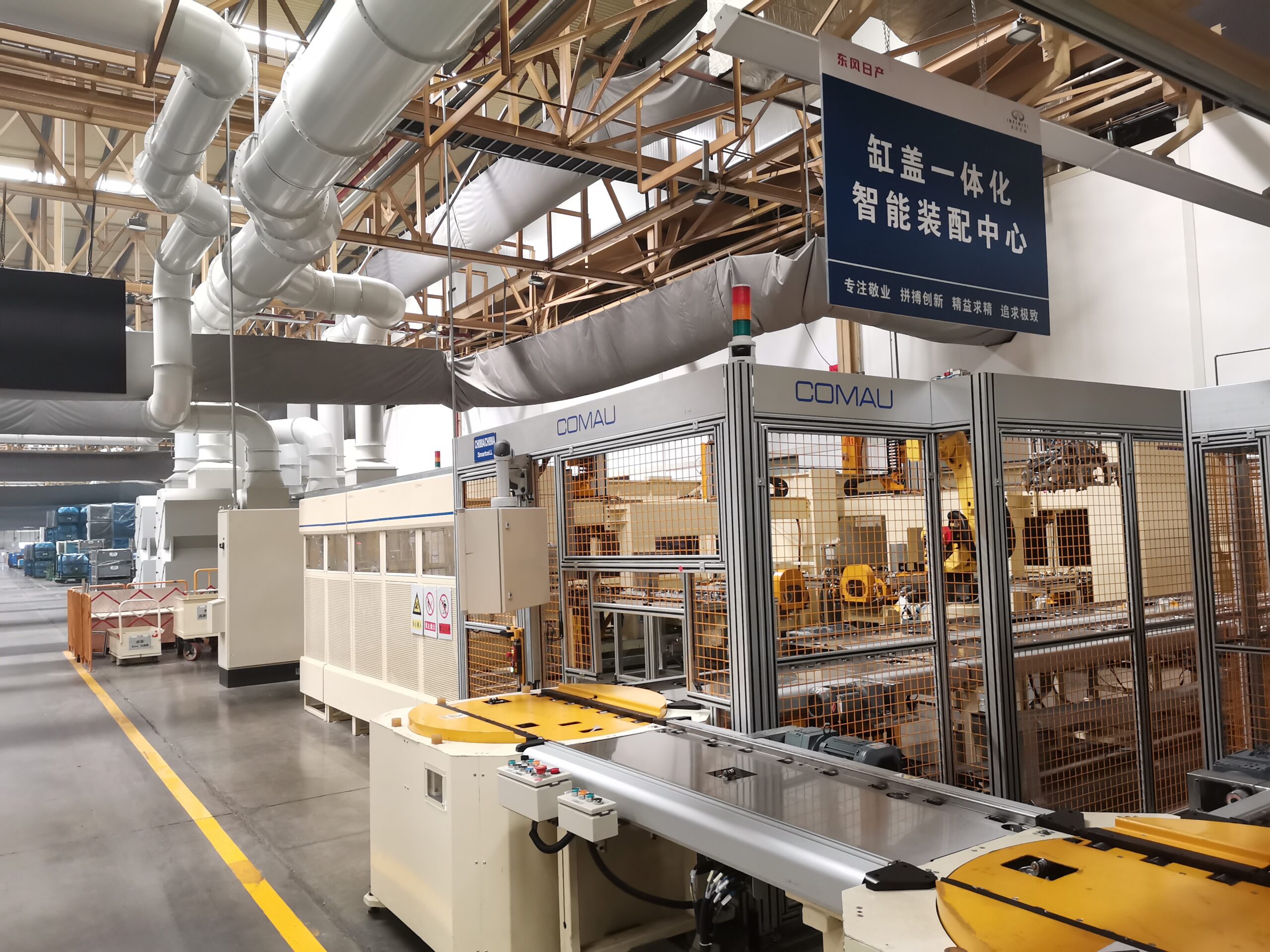
Os Resultados
Ao longo da implementação do projeto, diversas tecnologias avançadas foram aplicadas para resolver os vários desafios relacionados à produção dos novos motores Nissan. Ao mesmo tempo, o processo de design do projeto, através do uso do software de gerenciamento do ciclo de vida do produto, aproveitou recursos de digitalização, do design, produção e dos processos de fabricação. A digitalização de todo o projeto, permite à Nissan obter a transparência total do processo, controle de qualidade efetivo, redução dos riscos de projetos, custos de fabricação mais baixos, ciclo de produção mais curto e uma fonte importante de dados para a fabricação digital.
Ambos os modelos de motor entraram na produção em massa com sucesso, em agosto de 2020, com uma capacidade anual de 400.000 unidades. A solução da Comau também permite uma produção totalmente flexível. Quando equipamentos novos ou modificados são necessários, basta ajustar a programação do equipamento e as ferramentas de troca rápida para que o cliente consiga produzir modelos diferentes, aumentando a taxa de automação da fabricação do motor significativamente.
“A equipe da Comau demonstrou o valor da sua capacidade em sistemas de montagem e usinagem totalmente automatizadas. Eles dispunham dos recursos técnicos e da experiência de que precisávamos para manter esse projeto competitivo, tanto no orçamento como no cronograma”, disse Bai Zhongjin, Gerente de Projetos de Motores da Dongfeng Nissan.
k
motores por ano Capacidade de produção
modelos de motor distintos – coprodução eficiente
+
0%
de taxa de sucesso para as máquinas de carregamento único