Desenvolvendo tecnologias e processos avançados de produção
Com um histórico de sucesso no desenvolvimento de tecnologias avançadas e processos de produção no setor automotivo, a Comau do Brasil teve um papel importante no desenvolvimento do Fiat Pulse, primeiro SUV da marca feito no Brasil, e o Fiat Fastback, primeiro SUV Coupé e um dos principais lançamentos da marca para o mercado brasileiro.
A Comau recebeu o desafio de desenvolver estações automatizadas com alta capacidade produtiva nas operações Mainline; Bodysides e Respot para a produção dos dois SUVs, que deveriam ser produzidos na mesma linha de montagem. Em resposta a esse desafio, a Comau implementou uma solução avançada de montagem de carroceria, como parte de um projeto abrangente de retooling no Polo Automotivo Stellantis em Betim, Minas Gerais.
“Além de enfrentar os desafios relacionados à automação do projeto, a equipe da Comau foi ágil ao propor e integrar tecnologias de ponta para atender aos nossos objetivos de qualidade e tempo de ciclo. Este projeto, que é parte da nossa estratégia de Indústria 4.0, nos trouxe maior agilidade e flexibilidade para fabricar as diferentes versões do Fiat Pulse e Fiat Fastback e outros modelos, nas mesmas linhas de produção”.
Glauber Fullana, Vice-presidente de Manufatura da Stellantis South America
O Desafio
O desafio da Stellantis proposto à Comau era projetar uma solução tecnológica, que permitisse à empresa atender os objetivos de produção, qualidade e tempos de ciclo, utilizando uma plataforma já existente com flexibilidade suficiente para lidar com as variações de tamanho e especificações distintas dos dois modelos de SUV.
A Comau precisaria reequipar e remodelar as principais linhas de produção, garantindo uma manufatura eficiente, escalável, econômica e, ao mesmo tempo, lidar com as especificidades de outros modelos de veículos que são produzidos na mesma linha. Com segurança e flexibilidade como dois pilares essenciais do projeto, as linhas de montagem também deveriam otimizar a eficiência da automação com o mínimo de intervenções na linha.
Além de enfrentar as complexidades técnicas do projeto, a equipe da Comau também precisou lidar com um período de seis meses de paralisação, quando o projeto foi interrompido devido à pandemia de COVID-19.
A Solução
Sustentado por um conjunto de habilidades, resultado de décadas de experiência com o cliente, a Comau aproveitou sua presença local e expertise técnica nos diversos campos da Engenharia para atender aos requisitos mais complexos do projeto. O primeiro passo envolveu o trabalho conjunto com a Stellantis para fazer, de forma sustentável, o retooling de 74 estações automáticas e 10 estações manuais para as operações Mainline, Bodysides e Respot.
Mais especificamente, o time de Engenharia integrou os robôs de alta velocidade da Comau com sistemas de visão avançados, aplicação de adesivo industrial 3D, aplicações digitais e outros equipamentos na linha de produção para criar 3 operações principais: o sistema de manufatura Mainline (32 estações automáticas e 2 estações manuais); mais 28 estações automáticas e 6 estações de alimentação manual para a linha Bodysides; e a linha de montagem Respot (14 estações automáticas e 2 estações manuais). A solução abrangente de manufatura também inclui o sistema OpenGate, proprietário da Comau, que assegura a precisão geométrica e garante a flexibilidade necessária para lidar com a produção de múltiplas configurações, modelos diferentes de veículos e um tempo de ciclo agressivo de 52 segundos em média.
Para otimizar as etapas dessas linhas complexas, a Comau utilizou recursos de Comissionamento Virtual com simulação de processos, permitindo ao time testar a performance e funcionalidade das linhas, antes do comissionamento na fábrica. Ao fazer isso, a equipe foi capaz de antecipar eventuais problemas, tanto no sequenciamento dos robôs, como na comunicação entre robôs e PLC. Ao obter uma visão mais abrangente da planta, em um ambiente virtual, os engenheiros da Comau e da Stellantis conseguiram identificar pontos de melhorias, aprimorar o monitoramento dos processos e fazer o melhor uso do legado de equipamentos do Polo Automotivo – aspectos essenciais para uma maior eficiência de custos.
Outro ponto de destaque foi a utilização da tecnologia IO-Link para monitorar os fluxos de alimentação de água e ar comprimido, garantindo análises em tempo real e agilidade na detecção de eventuais problemas. A integração dos PLCs para otimizar as atividades de manutenção e a possibilidade de realizar atividades de backup dos programas de robôs via rede corporativa ajudam a proteger a confiabilidade de longo prazo de toda a linha.
Os Resultados
Como resultado de um trabalho conjunto entre a Stellantis e a Comau, as linhas remodeladas podem produzir as variações do SUV Fiat Pulse, e as variações do Fiat Fastback, incluindo o novíssimo Fastback Abarth. Todos compartilhando as mesmas estações de montagem, junto com outros modelos da marca.
Atendendo aos objetivos sustentáveis de reutilizar o máximo possível das plataformas originais, a Comau adicionou 17 novos robôs e 45 novas pinças de solda que, juntas, realizam 1000 pontos de solda na montagem em cada carroceria dos SUVs. A solução minimiza o processo de troca de ferramentas e a necessidade de intervenções nas linhas, com um impacto subsequente na sustentabilidade do projeto.
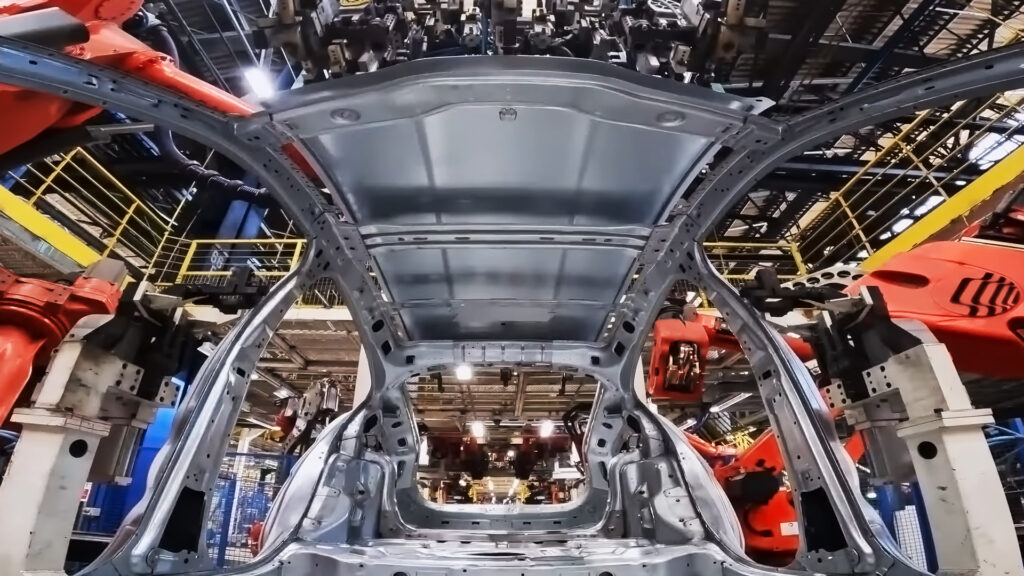
O profundo conhecimento em processos e a integração total com o time de Engenharia do cliente levaram a Comau a entregar o projeto com eficiência e dentro dos prazos estabelecidos. Com o projeto iniciado e os prazos de entrega assinados em outubro de 2019, o time foi forçado a paralisar o trabalho por 6 meses, no ponto alto da pandemia. No entanto, como os SUVs Pulse e Fastback seriam produzidos em conjunto com outros modelos da Fiat em linhas compartilhadas, o prazo para a finalização do projeto permaneceu inalterado. Com criatividade, compromisso com o cliente e o uso de Comissionamento Virtual com simulação de processos, o time da Comau foi capaz de otimizar os prazos de entrega, apesar do período em que o projeto precisou ser paralisado.
A solução inovadora desenvolvida pela Comau do Brasil com suporte de engenharia da Comau Romênia, reúne tecnologias avançadas e sistemas de visão que garantem os altos níveis de precisão requeridos pela Stellantis, tanto na geometria quanto na solda. Além disso, a solução oferece ao cliente equipamentos altamente eficientes e a flexibilidade para evoluir da produção em lotes para o modo de produção aleatório no futuro, de acordo com a necessidade produtiva. Esse projeto confirma o compromisso contínuo da Comau em fornecer soluções avançadas para manufatura flexível e contribuir para o desenvolvimento de veículos de qualidade para a indústria automotiva brasileira.”
estações automáticas em três linhas principais
estações manuais
pontos de solda por carroceria