Quando a Jeep estava preparando a fábrica para a produção do seu novo SUV, em uma das mais modernas plantas de manufatura automotiva, no estado de Pernambuco, as condições eram claras e diretas. A Comau seria responsável por expandir, de ponta a ponta, os sistemas de montagem de carroceria (funilaria) para possibilitar à montadora produzir seu novo SUV de 7 lugares – Jeep Commander – em um método de produção flexível, completamente alternado com 3 outros modelos já fabricados, garantindo a mesma capacidade produtiva de até 48 veículos por hora e que ainda poderia ser expandida no futuro.
Para incrementar o parque industrial, a Comau adicionou 24 novos robôs, 24 pinças de solda e 4 transportadores aos mais de 620 robôs de montagem e solda já instalados no polo automotivo Stellantis, em Goiana. Mais do que isso, as intervenções nas 14 linhas produtivas projetadas pela Comau, combinando operações automáticas, semi automáticas e manuais, foram realizadas durante o tempo de inatividade natural da planta para garantir o mínimo de impacto na produção.
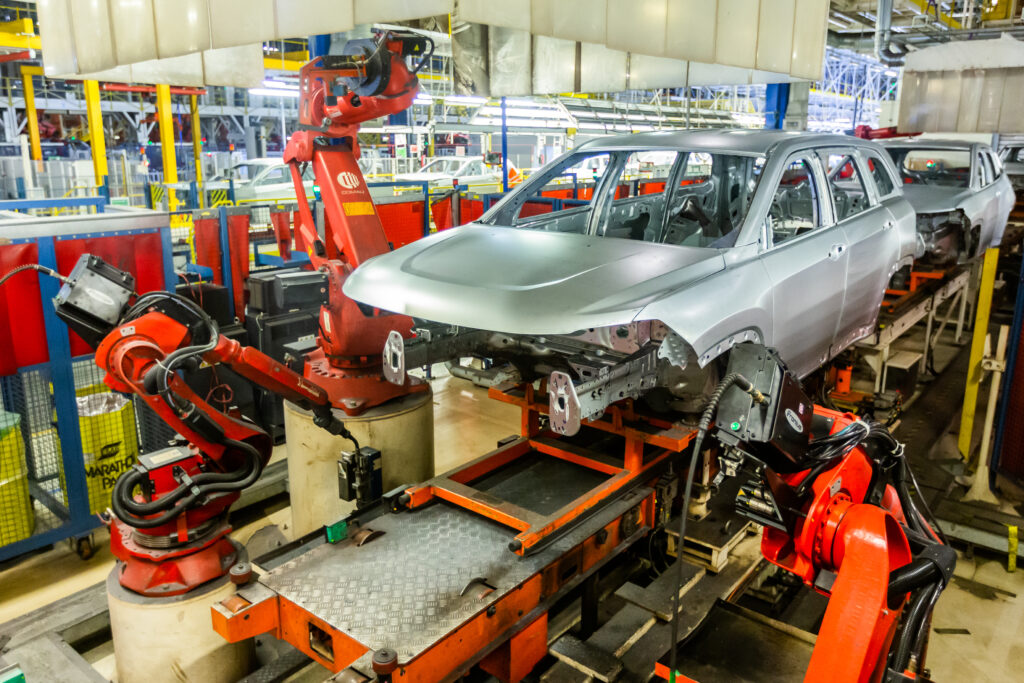
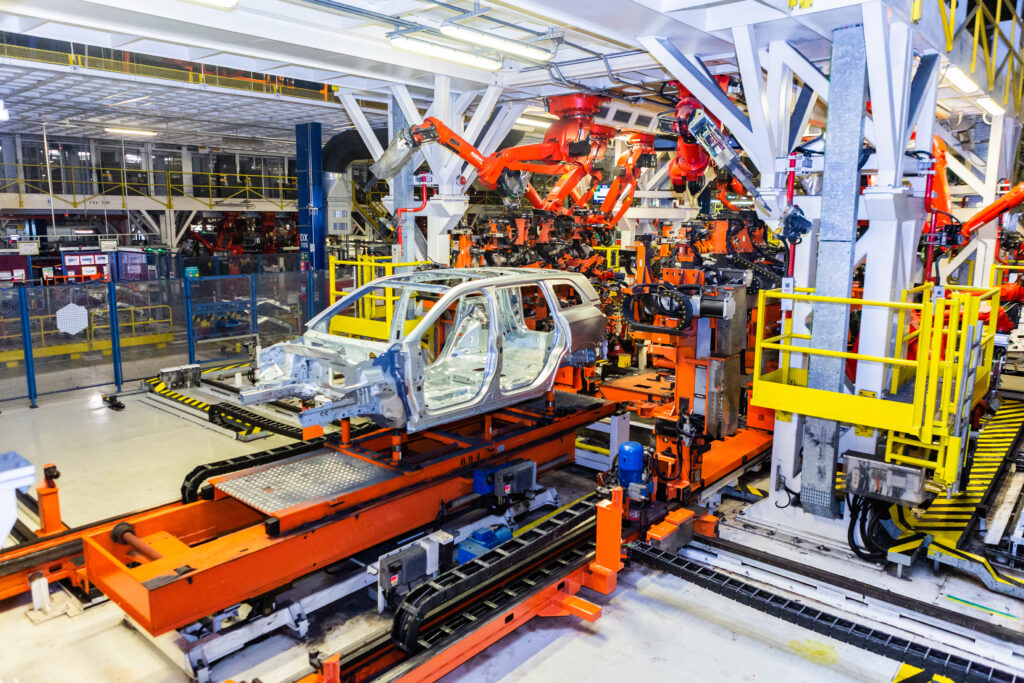
“Desde o início do projeto, a Comau demonstrou sua competência técnica, expertise em automação e comprometimento com o nosso sucesso”, explica Mateus Marchioro, Gerente da Planta Jeep. “Apesar da paralisação da fábrica por quase 2 meses, causada pela pandemia de COVID-19, a equipe conseguiu concluir todas as fases do projeto antes do previsto. Mais importante ainda, as soluções propostas demandam menos equipamentos auxiliares e menos processos manuais do que prevíamos inicialmente. Estamos contentes com o desempenho geral das novas linhas.“
Mateus Marchioro, Gerente da Planta Jeep
O Desafio
A Jeep desafiou a Comau a projetar uma solução inovadora que permitiria à montadora produzir seu mais novo SUV nas mesmas linhas de fabricação que estavam produzindo 3 dos veículos mais vendidos no Brasil em 2021, sem sacrificar a produção e tampouco os tempos de ciclo.
Aumentar o nível de automatização e melhorar a eficiência do processo era um desafio adicional, uma vez que as mudanças de ferramenta, necessárias de um modelo para outro, poderiam gerar ineficiências se não fossem projetadas cuidadosamente. Por fim, as linhas precisariam ter flexibilidade inerente para permitir que a Jeep introduza novos modelos no futuro.
O know-how técnico da Comau e a integração total com a equipe de engenharia da Jeep garantiram à montadora um projeto bem feito e realizado dentro do prazo. Depois de mapear os ciclos de produção reais, os engenheiros da Comau trabalharam com recursos de simulação para obter uma visão mais completa das modificações propostas no layout da linha de montagem, antes de qualquer implantação.
O diagnóstico preciso de onde e como os equipamentos e recursos estavam sendo utilizados, garantiu que todas as modificações, independentemente da origem, fossem representadas em um cenário digital.
Isso permitiu que a equipe otimizasse o comissionamento na planta e reduzisse ao mínimo o tempo de inatividade relacionado à implantação. A equipe também utilizou o comissionamento virtual com programação de simulação de processos para agilizar a implantação das linhas.
A Solução
Para atender as necessidades da Jeep em relação a flexibilidade de modelos, os engenheiros da Comau precisavam expandir a capacidade do inovador sistema Butterfly, de 3 modelos para 4 modelos, com a ordem de produção aleatória (random mix). Seria a primeira vez que o sistema, que é projetado em sua essência prevendo espaço físico para novos equipamentos e robôs quando novos modelos são introduzidos, lidaria com 4 modelos de veículos diferentes.
Em um ponto da linha, 14 robôs aplicam simultaneamente 100 pontos de solda em 52 segundos para unir as laterais e o chassi em uma operação única, garantindo uma geometria perfeita à carroceria. Em outro momento, 70 robôs aplicam adesivo estrutural para oferecer maior rigidez e maior resistência à infiltração de poeira e água. No total, cada veículo recebe mais de 3.000 pontos de solda durante o processo de montagem.
Outras modificações na linha incluem o aprimoramento do sistema automático de soldagem e montagem VersaRoll, da Comau. Ao fazer isso, a equipe de engenharia eliminou a necessidade de calibração do dispositivo e otimizou o número de robôs por estação.
Da mesma forma, o Tool Tray Shuttle, foi expandido para operar com 4 mesas pela primeira vez e, com isso, melhor se adaptar às necessidades específicas de montagem do novo SUV.
Para enfrentar os desafios relacionados à pandemia, que incluíam a impossibilidade de acessar a planta durante o período de fechamento mandatório, a Comau do Brasil adotou uma abordagem fluida de gerenciamento de projetos. A equipe trabalhou remotamente em Smart Working, aproveitando projetos de simulação de células e ferramentas de comissionamento virtual antes de passar para um retorno gradual e seguro das atividades na fábrica.
A equipe também precisou gerenciar atrasos na entrega de componentes e conseguiu fazer isso concentrando-se nas partes do projeto para as quais os suprimentos estavam disponíveis prontamente.
Como resultado, a Comau conseguiu se antecipar ao cronograma, implantando o projeto 598 em menos de 24 meses, do início ao fim. Mais importante, isso foi feito sem comprometer o fluxo e os volumes naturais de produção da planta Jeep, em Goiana.
Os Resultados
Com uma abordagem de manufatura enxuta, a solução inovadora da Comau é composta por uma alta proporção de processos avançados de automação, bem como a redução de equipamentos auxiliares. Câmeras são usadas para detectar peças por forma, em vez de sensores e fotocélulas. A digitalização completa 3D nas estações das linhas, garantiu perfeito alinhamento robótico.
Foram implementadas também soluções proprietárias da Comau, como solda a laser, sistemas de visão e o de grafagem Roller Hemming – RHEvo. Além disso, a configuração compatível com a Indústria 4.0 usa a tecnologia IO-link para ajudar a monitorar processos importantes, como os sistemas de água e ar comprimido e ajudar a detectar eventuais problemas de maneira rápida e altamente eficaz. Tudo isso proporciona à Jeep alta eficiência dos equipamentos e o aperfeiçoamento dos recursos de inspeção de qualidade.
Para ajudar a proteger a escalabilidade dos investimentos do cliente, todo o projeto foi desenvolvido para permitir que a Jeep introduza novos modelos no futuro. Além disso, o projeto liderado pelo Brasil representa a capacidade global da Comau de responder a desafios complexos, atendendo aos mais altos padrões de fabricação, com a colaboração direta de profissionais da Comau Romênia, Comau Itália e Comau China.
Dessa forma, a Comau do Brasil conseguiu alavancar sua presença local e expertise técnica de longa data em automação, digitalização e tecnologias inteligentes para entregar velocidade, qualidade e eficiência nas quais a Jeep pode confiar para produzir seus veículos premium.
modelos de veículos montados em um complexo de 14 linhas com ordem de produção aleatória
+
robôs Comau instalados
pontos de solda aplicados a cada 52 segundos