Oggi, “il picco di carbonio” e “la neutralità di carbonio” sono diventati obiettivi globali, con la Cina che dichiara chiaramente il suo obiettivo di “ottenere il picco di carbonio entro il 2030 e la neutralità di carbonio entro il 2060”. Guidate da questo obiettivo a lungo termine, le principali case automobilistiche si concentrano sul raggiungimento della conservazione dell’energia e della riduzione delle emissioni il prima possibile, oltre allo sviluppo e alla ricerca di nuove fonti di energia e all’introduzione di motori più efficienti, più ecologici e più economici dal punto di vista energetico. Nel 2018, Nissan ha lanciato il primo motore VC-Turbo prodotto in serie al mondo, un motore a rapporto di compressione variabile che bilancia la potenza e il consumo di carburante. La casa automobilistica è stata inoltre in grado di offrire un prezzo più competitivo sul mercato cinese localizzando la produzione.
“Il nostro modello 2.0T ha sia un motore a 4 cilindri in linea con rapporto di compressione variabile, sia un motore a 3 cilindri in linea con rapporto di compressione variabile e sovralimentazione turbo”, ha spiegato Chen Xiaosen, responsabile tecnico del motore di Dongfeng Nissan. “Per ragioni strategiche, scegliamo di produrre i due tipi di motori su una linea comune. Tuttavia, il metodo di produzione collineare impone requisiti più elevati sulla linea di produzione, sia per ottenere una lavorazione automatica, sia in termini di garantire un livello ragionevole di flessibilità.”
Chen Xiaosen, responsabile tecnico del motore di Dongfeng Nissan
La sfida
Nel gennaio 2019, Dongfeng Nissan ha incaricato Comau di progettare e implementare un sistema automatizzato di assemblaggio del motore ad alta velocità, che includesse le linee principali (assemblaggio della testata, assemblaggio del blocco corto, assemblaggio della biella del pistone, assemblaggio del motore nudo e linee di assemblaggio del motore), nonché le postazioni di lavoro di lavorazione non standard come le attrezzature di finitura della testata, le stazioni di carico e scarico robotizzate e i vassoi in dotazione.
Poiché il Nissan VC-Turbo Engine è il primo motore a rapporto di compressione variabile prodotto in serie a livello meccanico, e il suo progetto di lavorazione e assemblaggio intelligente sarebbe l’unica linea di produzione automatica intelligente in Cina a integrare il taglio dei metalli delle testate e il montaggio dei motori, Comau non ha potuto fare affidamento sui paradigmi di progettazione dei processi standard.
Per affrontare questa sfida, durante la progettazione e l’implementazione sono stati esplorati diversi processi chiave per la produzione del nuovo motore ad alta efficienza energetica grazie all’innovazione Comau nella tecnologia di automazione. La progettazione del processo dovrebbe anche tenere conto dei requisiti di alta qualità del cliente per i prodotti.
Un’ulteriore sfida riguardava il raggiungimento dell’obiettivo di elevata capacità produttiva del cliente, pari a 400.000 unità all’anno. A tal fine, Comau dovrebbe utilizzare contemporaneamente l’efficienza dell’industrializzazione e sfruttare le risorse per produrre prodotti personalizzati all’interno di un modello di business basato sulla lavorazione intelligente, il tutto tenendo conto delle condizioni di lavoro variabili e dell’assemblaggio delle linee di produzione su scala globale.
La soluzione
Per soddisfare i requisiti di qualità, produzione ed efficienza del cliente, Comau ha progettato una linea di produzione innovativa che applica una varietà di tecnologie avanzate di assemblaggio per l’automazione dei motori. Ciò include l’uso di robot a sette assi per la stazione di carico automatica della linea della testata, che sono in grado di afferrare un’ampia gamma di pezzi. Analogamente, l’uso di robot a sei assi per il serraggio automatico consente il posizionamento a più angolazioni per ottenere un serraggio automatico e flessibile. Con oltre 60 stazioni automatizzate lungo l’intera linea, la gamma di tecnologie di automazione e robotica è piuttosto ampia e ha consentito a Comau di applicare diverse delle sue soluzioni proprietarie come parte dei processi di assemblaggio chiave.
La tecnologia brevettata del centro di assemblaggio flessibile SmartCell di Comau è una di queste innovazioni. Integrando l’automazione dell’assemblaggio e la tecnologia dei centri di lavorazione in un unico centro di assemblaggio, il suo CNC multiasse (Computer Numerical Control) e la tecnologia di cambio rapido degli utensili offre un assemblaggio unico della testata. Ciò consente alla linea di assemblaggio del motore di gestire dinamicamente una varietà di processi di assemblaggio complessi, tra cui l’aggiornamento delle attività di assemblaggio che tradizionalmente vengono eseguite con la manodopera manuale a causa dell’elevato grado di difficoltà di automazione.
Il centro di assemblaggio flessibile SmartCell adotta robot a coordinate rettangolari (collegamento a 6 assi) per automatizzare completamente l’assemblaggio di tutte le parti della testa del motore, tra cui valvole in testa, guarnizioni dell’olio delle valvole, molle delle valvole, piastre di blocco delle valvole e sedi superiori. Per farlo, posiziona più set di dispositivi di assemblaggio automatici a cambio rapido e utilizza processi di assemblaggio paralleli, lavorando con robot a 6 assi, per completare il carico e lo scarico completamente automatizzati di testate di cilindri e pallet.
Inoltre, un innovativo metodo di press-fit flessibile e un sistema di posizionamento visivo consentono il carico automatico e una presa disordinata. Comau utilizza il sistema di posizionamento visivo del robot per rilevare la posizione del pezzo nel telaio del materiale e afferrarlo casualmente sul tavolo di alimentazione per la produzione di massa. Ciò garantisce una migliore efficienza produttiva, una maggiore flessibilità in termini di posizionamento del materiale in ingresso nella parte anteriore del robot e un rilevamento più rapido e preciso delle condizioni disordinate del materiale in ingresso. In futuro, quando si verificherà un cambio di modello o di prodotto, il cliente dovrà semplicemente aggiornare il programma anziché arrestare il sistema o reinvestire in nuove tecnologie. In questo modo si risparmiano i costi di manutenzione. Aspetto ancora più importante, tuttavia, è che la percentuale di guasti della linea può essere infinitamente ridotta a quasi zero, il che riduce notevolmente i costi di utilizzo successivi e il carico di lavoro del personale addetto alla manutenzione della linea. La linea di produzione è completata anche dal movimento del cilindro elettrico, dal cambio rapido della matrice di aggraffatura e dal movimento del pezzo, che può realizzare dinamicamente la pressatura flessibile di qualsiasi pezzo in qualsiasi posizione.
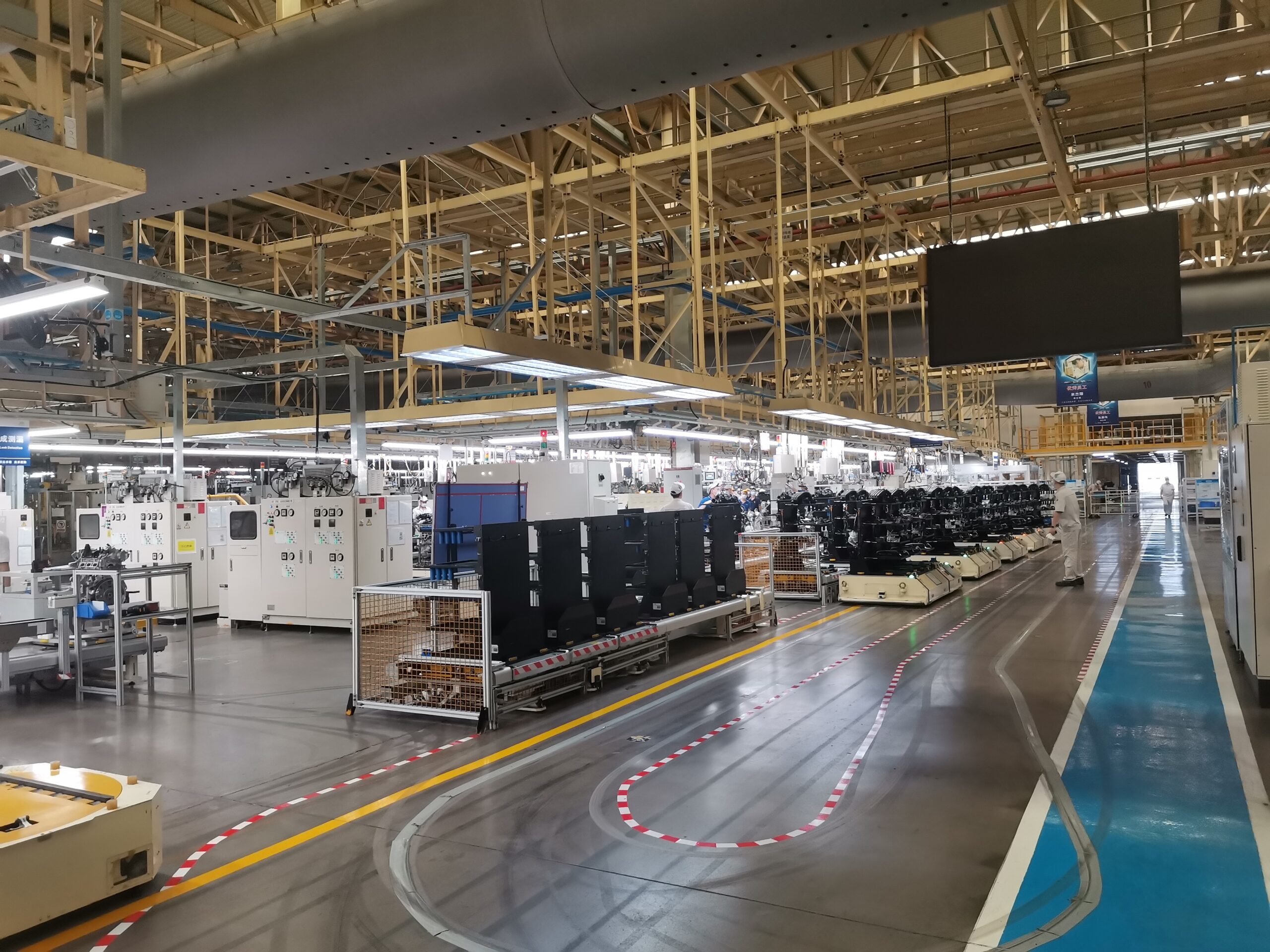
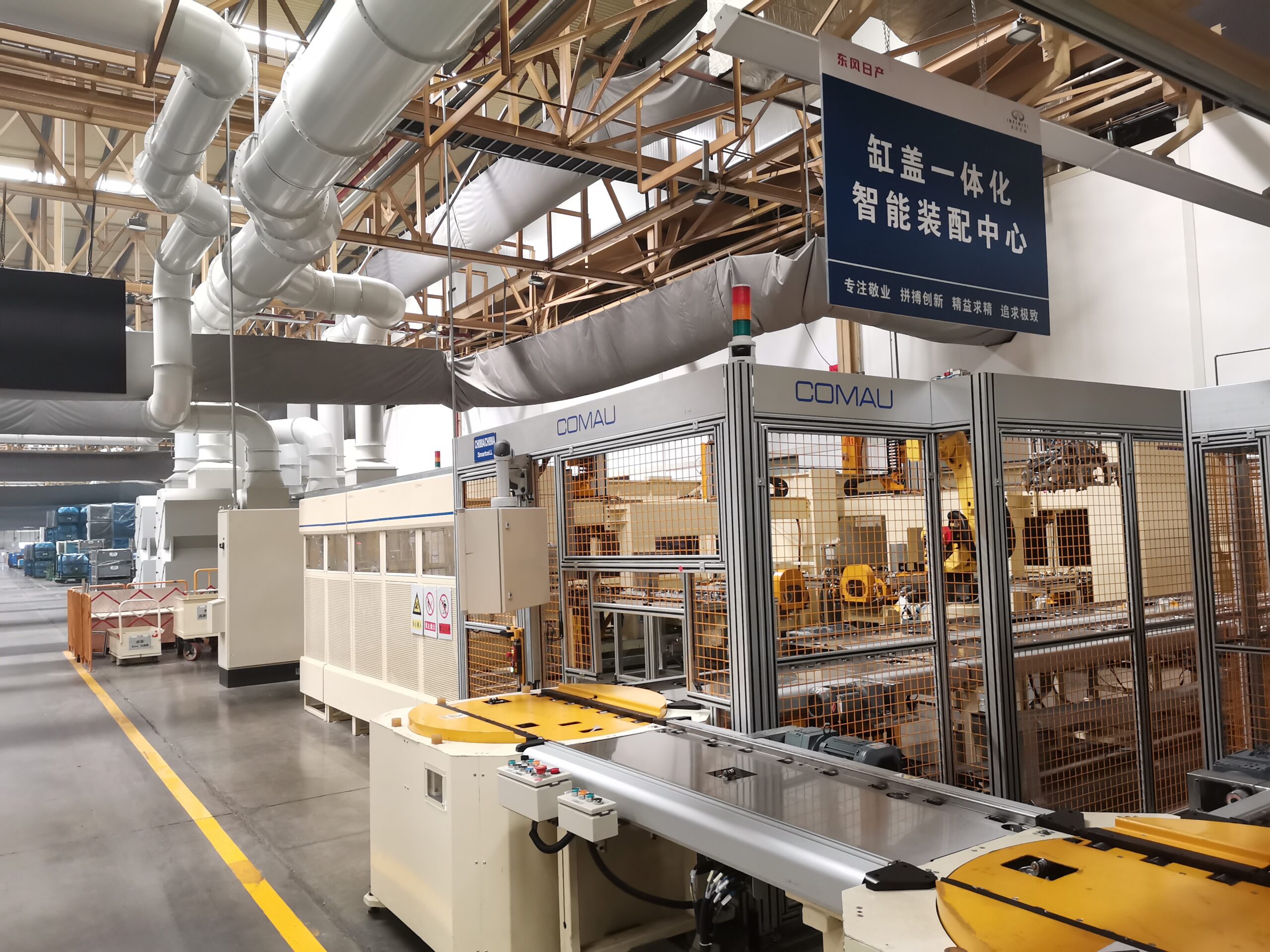
I risultati
Durante l’implementazione del progetto, sono state applicate diverse tecnologie avanzate per risolvere varie sfide relative alla produzione dei nuovi motori a risparmio energetico Nissan. Allo stesso tempo, il processo di progettazione, attraverso l’uso di software di gestione del ciclo di vita del prodotto, ha sfruttato la digitalizzazione dalla progettazione alla produzione. La digitalizzazione dell’intero processo di progettazione, produzione e fabbricazione e consente a Nissan di ottenere la piena trasparenza del processo, un efficace controllo della qualità di progettazione, minori rischi di progettazione, minori costi di produzione, un ciclo di produzione abbreviato e un’importante fonte di dati per la successiva produzione digitale.
Entrambi i modelli di motore sono entrati con successo nella produzione di massa nell’agosto 2020, con una capacità annua di 400.000 unità. La soluzione Comau consente inoltre una produzione completamente flessibile. Quando è necessaria un’apparecchiatura nuova o modificata, solo la programmazione dell’apparecchiatura e l’utensileria a cambio rapido devono essere adattate affinché il cliente possa godere di una produzione mista multi-modello, aumentando significativamente il tasso di automazione nella produzione di motori.
“Il team di Comau ha dimostrato il valore delle loro capacità uniche nell’assemblaggio e nella lavorazione completamente automatizzati. Aveva i sistemi tecnici e la vasta esperienza di cui avevamo bisogno per mantenere questo progetto competitivo sia in termini di budget che di tempi,”ha dichiarato Bai Zhongjin, Dongfeng Nissan Engine Project Manager.
K
unità all’anno come capacità di produzione
diversi modelli di motore coproduzione efficiente
+
0%
tasso di successo per le singole macchine di carico