Tecnologie e processi produttivi avanzati
Con una comprovata esperienza nello sviluppo di tecnologie e processi produttivi avanzati per il settore automobilistico, Comau Brasile ha svolto un ruolo chiave nello sviluppo sia del nuovo Fiat Pulse, il primo modello SUV del marchio in Brasile sia del Fiat Fastback, il primo SUV Coupé del marchio e uno dei principali lanci di Fiat nel 2022 per il mercato locale.
Comau è stata incaricata di sviluppare una linea di produzione automatizzata ad alto volume per la scocca, le fiancate e le operazioni di respot per i due SUV, che avrebbero dovuto essere entrambi prodotti sulla stessa linea di assemblaggio. In risposta, Comau ha implementato le sue soluzioni avanzate di assemblaggio della carrozzeria nell’ambito di un progetto di retooling completo presso lo stabilimento automobilistico Stellantis di Betim – Minas Gerais.
“Oltre ad affrontare le sfide intrinseche dell’automazione, il team Comau è stato veloce nel proporre e integrare tecnologie chiave per soddisfare i nostri obiettivi di qualità e tempi ciclo. Questo progetto, che fa parte della nostra strategia per l’Industria 4.0, ci ha fornito maggiore agilità e la flessibilità per produrre diverse versioni e altri modelli sulle stesse linee”
Glauber Fullana, Vicepresidente della Produzione di Stellantis South America
La sfida
Stellantis ha sfidato Comau a progettare una soluzione all’avanguardia che consentisse all’azienda di raggiungere i suoi obiettivi di produzione, gli obiettivi di qualità e i tempi ciclo, utilizzando una piattaforma preesistente con una flessibilità sufficiente per gestire le dimensioni uniche e le variazioni delle specifiche dei due distinti modelli SUV.
Inoltre, Comau avrebbe dovuto riattrezzare e ristrutturare sia le linee principali che quelle di respot, per garantire una produzione su larga scala e conveniente di molteplici varianti di modello, garantendo al contempo la continuità della produzione per le autovetture e i camion con cui le linee sarebbero state condivise. Poiché la sicurezza e la flessibilità sono due pilastri essenziali del progetto, le linee di assemblaggio avrebbero dovuto anche ottimizzare l’efficienza dell’automazione con interventi minimi sulla lineai.
Infine, oltre a gestire le elevate complessità tecniche del progetto, il team Comau si è trovato ad affrontare un’interruzione di sei mesi poiché il progetto è stato interrotto a causa della pandemia di COVID-19.
La soluzione
Supportata da una solida serie di competenze derivate da decenni di esperienza con il cliente, Comau ha sfruttato la sua presenza locale e il suo know-how tecnico in diversi campi ingegneristici per soddisfare le richieste esigenti del progetto. Il primo passo è stato quello di lavorare direttamente insieme alla casa automobilistica per riattrezzare e ristrutturare in modo sostenibile un totale di 74 stazioni automatiche e 10 stazioni manuali per la linea principale dei SUV, le finacate della carrozzeria e le attività di respot.
Più nello specifico, il team tecnico ha integrato i robot industriali ad alta velocità Comau con sistemi di visione avanzati, erogazione di adesivi 3D, applicazioni digitali e attrezzature chiavi in mano per creare 3 stazioni di attività principali: il sistema di produzione principale (32 stazioni automatiche e 2 stazioni manuali); 28 stazioni automatiche aggiuntive e 6 linee di carico manuale per la linea di assemblaggio fiancata carrozzeria; e la linea di assemblaggio respot (14 stazioni automatiche e 2 manuali). La soluzione di produzione completa presenta anche il sistema OpenGate di Comau, che garantisce la precisione geometrica, garantendo al contempo la flessibilità intrinseca per gestire più configurazioni di modello e un tempo ciclo medio aggressivo di 52 secondi.
Per ottimizzare la progettazione e il retooling delle linee complesse, Comau ha utilizzato le capacità di messa in servizio virtuale e la simulazione del processo, consentendo al team di testare le prestazioni e le funzionalità previste prima della messa in servizio in loco. In tal modo, il team è stato in grado di anticipare eventuali problemi in termini di sequenziamento dei robot e di comunicazione tra robot e PLC. Avere una visione completa dell’impianto virtuale ha inoltre consentito agli ingegneri di Comau e Stellantis di identificare i punti di miglioramento, migliorare il monitoraggio dei processi e utilizzare meglio le attrezzature dell’impianto esistente, oltre a ottimizzare l’intralogistica tra le stazioni e le linee. Tutte queste caratteristiche, insieme, sono aspetti essenziali per un approccio efficace dal design al costo.
Un’altra caratteristica importante è l’uso della tecnologia IO-Link per monitorare il sistema di alimentazione dell’acqua e dell’aria compressa, garantendo analisi in tempo reale e un rilevamento agile dei problemi. L’integrazione del software PLC contribuisce anche a ottimizzare le attività di manutenzione e la possibilità di eseguire il backup delle attività dei robot tramite la rete aziendale garantisce un’affidabilità a lungo termine sull’intera linea.
I risultati
Frutto del lavoro congiunto di Comau e Stellantis, le linee rinnovate hanno permesso a Stellantis di assemblare in serie 5 varianti del suo nuovo SUV Pulse, tra cui il Pulse Abarth, e 2 varianti del SUV Fastback, incluso il modello Fastback Abarth, il tutto con una condivisione delle postazioni di assemblaggio con altri modelli Fiat.
Per raggiungere l’obiettivo di sostenibilità di riutilizzare quanto più possibile della piattaforma originale, Comau ha aggiunto 17 nuovi robot e 45 nuove pinze di saldatura che insieme gestiscono un totale di fino a 1000 punti di saldatura per la carrozzeria e le fiancate dei SUV. La soluzione riduce al minimo anche i cambi di utensile e gli interventi sulla linea, facendo risparmiare tempo e influendo positivamente sulla sostenibilità complessiva del progetto.
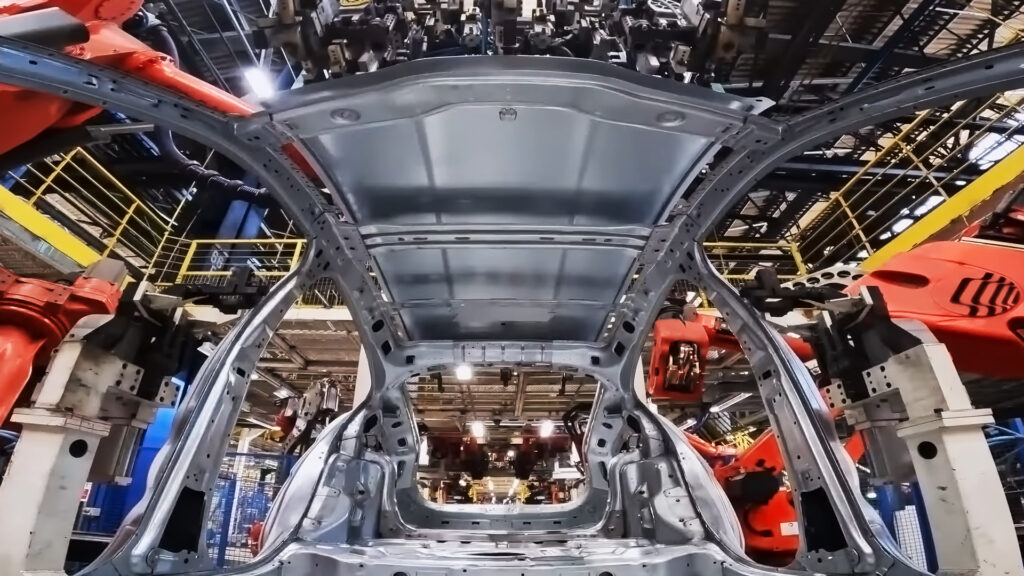
La profonda conoscenza dei processi di Comau e la sua completa integrazione con il team di progettazione del cliente hanno consentito loro di consegnare il progetto in modo efficiente e puntuale. Dopo aver firmato le date previste per la consegna nell’ottobre 2019, il team è stato costretto a interrompere il lavoro per 6 mesi durante la pandemia sanitaria globale. Tuttavia, poiché Pulse e Fastback sarebbero stati prodotti insieme ad altri modelli Fiat su linee condivise, non è stato possibile modificare la data di lancio originale. Grazie alla creatività, all’impegno e all’uso della messa in servizio virtuale e della simulazione di processo di Comau, il team è stato in grado di ottimizzare gli obiettivi di consegna in loco nonostante l’arresto inatteso del progetto.
La soluzione innovativa è stata sviluppata da Comau Brasile con il supporto ingegneristico di Comau Romania, le cui avanzate tecnologie di sistema di visione garantiscono la precisione estetica della geometria e la precisione di saldatura richieste da Stellantis. Inoltre, la soluzione offre al cliente una migliore efficienza delle attrezzature e la flessibilità necessaria per passare dalla produzione in lotti alla produzione in miscela casuale in futuro, secondo necessità. Infatti, il progetto testimonia il costante impegno di Comau a fornire soluzioni di produzione avanzate e a contribuire allo sviluppo di veicoli di qualità per l’industria automobilistica brasiliana.
stazioni automatiche su tre linee principali
stazioni manuali
punti di saldatura per la carrozzeria