Technologies avancées et des processus de production
Comau Brésil, qui développe avec succès des technologies avancées et des processus de production pour le secteur automobile, a joué un rôle essentiel dans la mise au point du nouveau Fiat Pulse, premier modèle de SUV de la marque au Brésil, et du Fiat Fastback, premier SUV coupé de la marque et l’un des principaux lancements de Fiat en 2022 sur le marché local.
Comau a été chargé de développer une chaîne automatisée de production de masse pour la carrosserie principale, les flancs et les opérations de finition de caisse des deux SUV, qui devaient tous deux sortir de la même chaîne d’assemblage. À cet effet, Comau a déployé ses solutions perfectionnées d’assemblage de carrosserie dans le cadre d’un projet de rééquipement complet à l’usine automobile Stellantis de Betim, dans le Minas Gerais.
« En plus de relever les défis d’automatisation inhérents au projet, l’équipe de Comau a rapidement proposé et intégré des technologies clés pour atteindre nos objectifs de qualité et de temps de cycle. Ce projet, qui rentre dans le cadre de notre stratégie d’industrie 4.0, nous a apporté plus d’agilité et de flexibilité dans la production de différentes versions et différents modèles sur les mêmes chaînes. »
Glauber Fullana, vice-président de la production de Stellantis Amérique du Sud
Défi
Stellantis a demandé à Comau de concevoir une solution de pointe qui lui permette d’atteindre ses objectifs de production, de qualité et de temps de cycle, en utilisant une plateforme préexistante suffisamment souple pour gérer les variations de dimensions et de spécifications des deux modèles de SUV.
De surcroît, Comau devait rééquiper et rénover tant la chaîne principale que les chaînes de finition de caisse, afin d’assurer une production rentable à grande échelle de multiples variantes des modèles, tout en garantissant la continuité de la production des voitures et pick-ups avec lesquels les chaînes seraient partagées. La sécurité et la flexibilité étant deux piliers essentiels du projet, les chaînes d’assemblage devaient également optimiser l’efficience de l’automatisation et n’impliquer que des interventions minimales.
Enfin, outre la complexité technique du projet, l’équipe de Comau a été confrontée à la pandémie de COVID-19, qui a mis le projet au point mort pendant six mois.
Solution
Fort de ses solides compétences, acquises pendant des décennies d’expérience auprès de son client, Comau a tiré parti de sa présence locale et de son savoir-faire technique dans différents domaines pour répondre aux exigences élevées de ce projet. La première étape a consisté à travailler directement aux côtés du constructeur automobile pour rééquiper et rénover durablement 74 postes de travail automatiques et 10 postes manuels, intervenant sur la chaîne principale, les flancs de la carrosserie et dans les activités de finition des SUV.
Plus précisément, l’équipe d’ingénieurs a intégré les robots industriels à grande vitesse de Comau – avec systèmes de vision avancés, distribution d’adhésif en 3D, applications numériques et équipement clés en main – pour créer trois postes d’activité principaux : le système de production de la chaîne principale (32 postes automatiques et deux postes manuels), 28 postes automatiques supplémentaires et six lignes de chargement manuel pour la chaîne d’assemblage des flancs de la carrosserie et la chaîne de finition de l’assemblage (14 postes automatiques et deux postes manuels). La solution de production comprend également le système OpenGate de Comau, qui garantit l’exactitude géométrique et la flexibilité indispensable à la gestion de plusieurs configurations de modèles et assure un temps de cycle extrêmement court, à savoir 52 secondes en moyenne.
Afin d’optimiser la conception et le rééquipement des chaînes complexes, Comau a utilisé des capacités de mise en service virtuelle et de simulation des processus, qui ont permis à l’équipe de tester les performances et les fonctionnalités attendues avant le démarrage réel de l’équipement. L’équipe a ainsi pu anticiper d’éventuels problèmes de séquencement des tâches robotisées et de communication entre les robots et le PLC. La vue complète de l’usine virtuelle a également permis aux ingénieurs de Comau et Stellantis d’identifier les points à améliorer, de perfectionner la surveillance des processus et de mieux utiliser l’équipement existant, ainsi que d’optimiser l’intralogistique entre les postes et les chaînes. Toutes ces caractéristiques combinées sont essentielles à une démarche efficace de conception à coût objectif.
Autre fait saillant, la technologie IO-Link sert à surveiller le système d’alimentation en eau et en air comprimé et garantit une analyse en temps réel et une détection rapide des problèmes. L’intégration d’un logiciel de PLC contribue également à optimiser les activités de maintenance et la possibilité de sauvegarder les activités du robot via le réseau de l’entreprise assure la fiabilité à long terme de l’ensemble de la chaîne.
Résultats
Grâce au travail conjoint de Comau et Stellantis, les chaînes remaniées ont permis à Stellantis d’assembler par lots cinq variantes de son nouveau SUV Pulse, dont le Pulse Abarth, et deux variantes du SUV Fastback, y compris le modèle Fastback Abarth, tout en partageant les postes d’assemblage avec d’autres modèles Fiat.
L’objectif de durabilité étant de réutiliser autant que possible la plateforme d’origine, Comau a ajouté 17 nouveaux robots et 45 nouveaux pistolets de soudage qui, ensemble, gèrent un total de 1 000 points de soudage sur la carrosserie principale et les flancs des SUV. Par ailleurs, la solution apportée minimise les changements d’outils et les interventions sur la chaîne, ce qui fait gagner du temps et améliore la durabilité globale du projet.
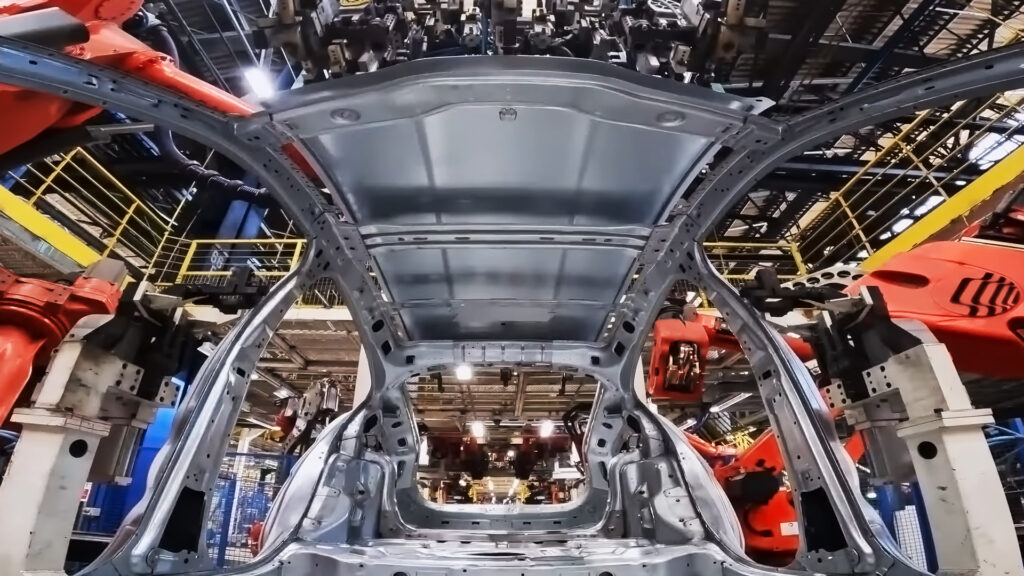
L’intégration complète de Comau dans l’équipe d’ingénierie du client et sa connaissance approfondie des processus lui ont permis de réaliser le projet de manière efficiente et dans les délais prévus. Après avoir accepté les jalons de livraison en octobre 2019, l’équipe a été contrainte d’arrêter le travail pendant six mois au plus fort de la pandémie mondiale. Cependant, comme le Pulse et le Fastback devaient être produits en même temps que d’autres modèles Fiat sur des chaînes partagées, il était impossible de modifier la date de lancement initiale. Grâce à la créativité et la détermination de Comau, qui a fait appel à la mise en service virtuelle et à la simulation des processus, l’équipe a pu optimiser les objectifs de livraison sur place malgré l’arrêt inattendu du projet.
La solution innovante a été élaborée par Comau Brésil avec le soutien technique de Comau Roumanie, dont les technologies sophistiquées de système de vision garantissent l’esthétique exacte de la géométrie et la précision de soudage exigées par Stellantis. De plus, la solution offre au client un équipement plus efficient et la flexibilité nécessaire pour passer d’une production par lots à une production en mélange aléatoire à l’avenir, si nécessaire. Le projet témoigne de l’engagement continu de Comau à fournir des solutions de production avancées et à contribuer au développement de véhicules de qualité pour l’industrie automobile brésilienne.
postes automatiques sur trois chaînes principales
postes manuels sur trois chaînes principales
points de soudage sur la carrosserie principale