À l’époque où Jeep se préparait à produire son nouveau SUV dans l’une des usines automobiles les plus modernes de l’état brésilien du Pernambouc, l’entreprise avait des exigences claires et précises. Comau était chargée d’agrandir les systèmes d’assemblage de la carrosserie pour permettre au constructeur de produire son nouveau SUV Jeep Commander à sept places selon une méthode flexible, en alternance avec trois autres modèles déjà fabriqués, tout en garantissant la même capacité de production de 48 véhicules par heure (capacité susceptible d’être augmentée par la suite). Comau a ajouté 24 robots, 24 pinces de soudage et quatre tapis convoyeurs à plus de 620 robots de montage et de soudage déjà installés dans l’usine Jeep à Goiana. En outre, les interventions sur les 14 lignes de production prévues par Comau, associant des opérations automatisées, semi-automatisées et manuelles, ont été réalisées pendant la période d’inactivité normale de l’usine, afin d’avoir le plus faible impact possible sur la production.
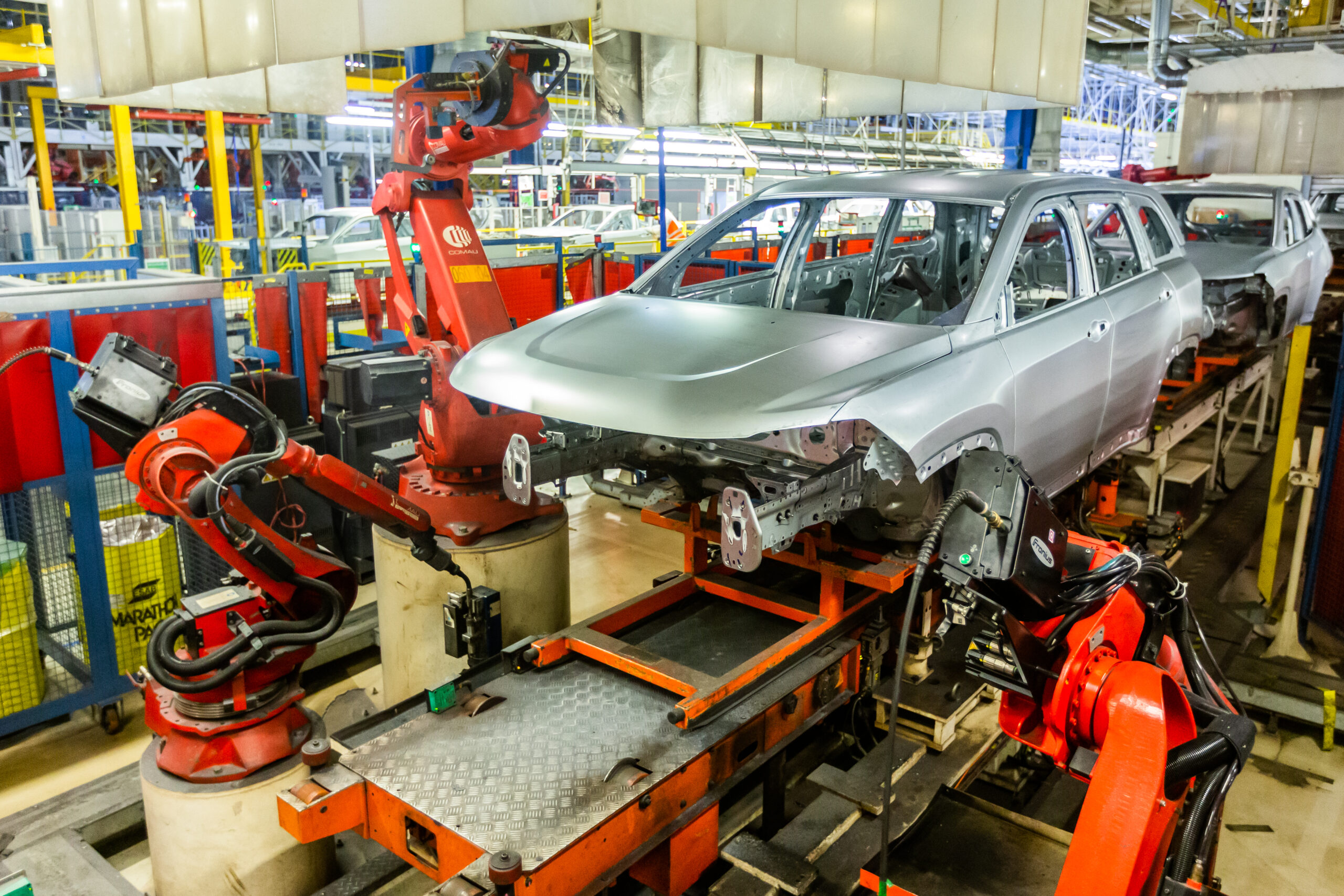

« Dès le début du projet, Comau a fait la preuve de ses compétences techniques, de son expertise en termes d’automatisation et de son engagement envers notre réussite », indique Mateus Marchioro, gérant de l’usine Jeep Brazil. « Malgré l’arrêt de l’usine pendant presque deux mois, à cause de la pandémie de COVID-19, l’équipe est parvenue à terminer toutes les phases du projet en avance. Le plus important est que les solutions proposées demandent moins de matériel auxiliaire et de procédés manuels qu’anticipé. Nous sommes satisfaits des performances générales des nouvelles lignes. »
Mateus Marchioro, gérant de l’usine Jeep Brazil.
Défi
Jeep a mis Comau au défi de concevoir une solution innovante lui permettant de produire son nouveau SUV sur les lignes qui produisaient déjà trois des véhicules les plus vendus au Brésil, sans sacrifier les objectifs de production ou les temps de cycle. L’amélioration du niveau d’automatisation et du rendement du processus constituait un défi supplémentaire, car le changement d’outil entre les modèles était susceptible d’entraîner un manque d’efficacité s’il n’était pas soigneusement étudié. Enfin, les lignes de fabrication devaient être intrinsèquement flexibles pour permettre à Jeep de fabriquer de nouveaux modèles à l’avenir.
Le savoir-faire technique de Comau et son intégration complète au sein de l’équipe d’ingénierie de Jeep garantissaient au constructeur la bonne réalisation du projet dans les délais prévus. Après l’établissement des cycles de production réels, les ingénieurs de Comau ont travaillé avec des outils de simulation pour brosser un tableau plus complet des modifications d’implantation de la ligne d’assemblage avant toute mise en œuvre. Le diagnostic précis de l’utilisation de l’équipement et des ressources a abouti à un scénario numérique représentant toutes les modifications, indépendamment de leur origine. L’équipe a ainsi pu optimiser la mise en service de l’installation et réduire le plus possible le temps d’arrêt lié à la mise en œuvre. L’équipe a également recouru à la mise en service virtuelle et simulé les procédés pour accélérer la mise en service des lignes.
high-volume production targets. The joint engineering team also faced unique technical and process challenges, including optimization of the magnetic block insertion and rotor injection activities, in addition to various automation issues related to high-speed loading, assembly and test phases.
Solution
Afin de répondre aux besoins de Jeep en termes de flexibilité, les ingénieurs de Comau ont dû augmenter la capacité du système Butterfly innovant et la faire passer de trois à quatre modèles, avec un ordre de production aléatoire. Pour la première fois, le système peut gérer quatre modèles de véhicules différents. Il prévoit de la place pour l’équipement et les robots qui devront être installés lors de la production future de nouveaux modèles. En un point de la ligne, 14 robots effectuent simultanément 100 points de soudure en 52 secondes, afin d’assembler les flancs et le châssis en une seule opération, tout en assurant la géométrie parfaite de la carrosserie. Ailleurs, 70 robots appliquent un adhésif structurel qui accentue la rigidité et la résistance à l’infiltration de poussière et d’eau. Au total, chaque véhicule reçoit plus de 3 000 points de soudure pendant le processus d’assemblage.
Les autres modifications de la ligne sont notamment l’amélioration du système de soudage et d’assemblage automatique, VersaRoll. Le dispositif n’a plus besoin d’être étalonné et le nombre de robots par poste est optimisé. La navette de desserte d’outils a été agrandie pour comporter quatre tables et mieux s’adapter aux besoins particuliers d’assemblage du nouveau SUV.
Pour relever les défis liés à la pandémie, parmi lesquels l’impossibilité d’accéder à l’usine pendant le confinement obligatoire, Comau Brésil a adopté une démarche fluide de gestion de projet. L’équipe a travaillé à distance en « smart working » et utilisé des simulations de cellules et des outils de mise en service virtuelle avant de revenir progressivement à des activités sur place, de manière sécurisée. L’équipe a également dû gérer les retards de livraison des composants. Elle y est parvenue en se focalisant sur les parties du projet pour lesquelles les fournitures étaient disponibles en temps opportun. De ce fait, Comau est restée en avance sur le calendrier et a déployé le Projet 598 en moins de 24 mois, du début à la fin. La cadence et les volumes naturels de production de l’usine Jeep de Goiana n’ont pas eu à en souffrir, un véritable tour de force.
Résultats
Suivant une démarche de fabrication rationalisée, la solution innovante de Comau bénéficie d’une grande proportion de procédés perfectionnés d’automatisation et implique moins d’équipement auxiliaire. Des caméras, qui remplacent les capteurs et cellules photoélectriques, détectent les pièces en fonction de leur forme. La numérisation tridimensionnelle complète des postes de la ligne garantit l’harmonisation parfaite des robots. Des solutions propres à Comau, telles que le soudage laser, les systèmes de visualisation et le sertissage à la molette RHEvo, ont également été mises en place. En outre, la configuration compatible avec l’industrie 4.0 utilise la technologie IO-Link pour surveiller les processus clés, par exemple, les circuits d’eau et d’air comprimé, et détecter les éventuels problèmes de manière rapide et extrêmement efficace. Tout cela offre à Jeep un rendement élevé de l’équipement et améliore le contrôle de la qualité.
Afin de protéger la pérennité de l’investissement, tout le projet a été conçu pour permettre à Jeep de produire de nouveaux modèles sur ces lignes. Par ailleurs, le projet mené par Comau Brésil reflète la capacité mondiale de Comau à relever des défis complexes tout en respectant les normes de fabrication les plus exigeantes, avec la collaboration directe de Comau Roumanie, Comau Italie et Comau Chine. Comau Brésil a su exploiter sa présence locale et sa longue expertise en automatisation, numérisation et technologies intelligentes pour offrir à Jeep la vitesse, la qualité et l’efficacité nécessaires à la production de ses véhicules haut de gamme.
modèles de véhicules assemblés dans une installation de 14 lignes, avec un ordre de production aléatoire
+
robots Comau installés
points de soudure appliqués toutes les 52 secondes
perte de productivité pendant le processus d’agrandissement