Being good isn’t enough
When it comes to automation, few can top Comau’s expertise and winning track record. Yet electrification is a new ballgame, where being good is just the first step. This is why we leverage the Comau DNA and team-driven approach to cover the entire e-value chain with real answers to a vast range of real project scenarios.
With an entire portfolio of innovative products and process technologies to support electricity supply transformation and utilization, we are paving the way to electrification with modular, scalable and investment-effective solutions. What’s more, our worldwide team of over 200 dedicated resources and 3 research centers have helped more than 40 companies around the globe advance their electrification strategies.
AI-based assurance
When it comes to verifying the efficiency of E-power solutions, Comau’s proprietary automated testing and control paradigm is without equal. The non-invasive process, which is based on the in-line acquisition of thermal images, accurately verifies electrical resistance and joint quality of each single joint in a fast and efficient manner. By assessing the quality of each joint before final assembly, manufacturers can ensure battery safety and prevent waste. And because the solution does not require its own power source, it can be added to any industrial battery manufacturing line without affecting cycle time or the manufacturing layout.
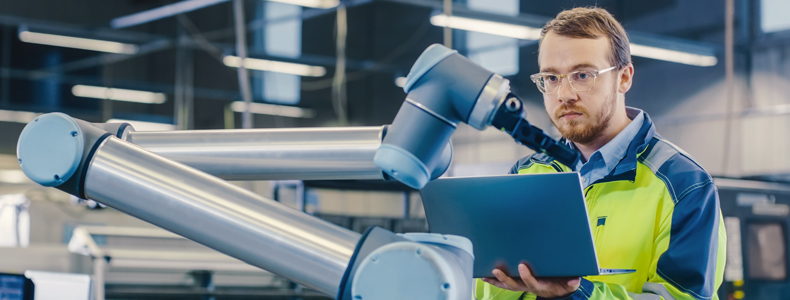
Automating outdoor installation
One of the best things about innovative engineering is finding solutions to previously unidentified problems. Take Hyperion for example, a unique mobile outdoor installation system that Comau designed to transport, manipulate and autonomously install 30 kg solar panels in the open field under virtually any condition.
The solution is a perfect example of Comau’s approach to open automation. In recognizing the possibility to industrialize a manual process, Comau worked closely with the customer to design, develop and deploy a mobile installation system – featuring an automated crawler vehicle and heavy-payload articulated robot – in just under 7 months. Today, the complete, ready-to-use mobile installation system can be easily deployed within both new and existing solar fields to simplify the deployment of photovoltaic plants and limit the operations that workers would need to perform in harsh outdoor conditions like heavy rain and high/low temperatures.
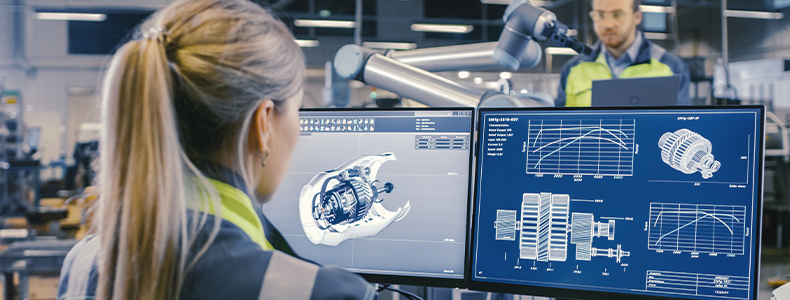
Batteries for ships
Unlike the high-volume, standardized automation in the automotive industry, battery manufacturing is similar to niche-production in that no two modules are exactly the same. Until recently, battery manufacturing for heavy transportation, naval and rail was a largely manual process, driven by the need to address a series of inherent variances stemming from final use requirements.
Working with one of the world’s leading naval electric power solutions providers, Comau has industrialized the lithium-ion battery cell manufacturing process with end-to-end automation based on an innovative welding environment where robotics, laser welding, AI and the automatic validation of mechanical and electrical resistance combine to ensure multi-module configuration flexibility of high-performance battery modules.