Overcoming Challenges
in Welding Operations
Meeting high production targets while maintaining exceptional welding quality and safety standards can be a challenge for manual welding operations. The inconsistency of weld quality, labor shortages, and safety risks posed by hazardous conditions and temperature control are major concerns. Additionally, environmental factors and high operating costs for consumables, equipment, and labor can impact productivity.
Demand saturation can create production bottlenecks, impacting quality and delivery times. These challenges are particularly significant in industries where productivity and efficiency are paramount to success. Comau’s robotic arc welding solutions are designed to meet these challenges, ensuring that operations remain efficient, safe, and cost-effective.
Benefits of Switching to
Automated Arc Welding
Reduced defects
Our automated systems ensure uniformity across every weld, reducing defects and minimizing costly rework.
Increased Productivity
Robotic welders work faster and with greater precision, significantly boosting production rates.
Improved Safety
By automating hazardous tasks, you protect your workforce from dangerous conditions, reducing accident risks and associated downtime
Process efficiency
Automated welding optimizes material use, minimizes waste by using only the necessary amount of consumables like gas and wire
Automating Arc Welding processes with Comau’s advanced robotic solutions effectively addresses these gaps. Unlike manual operations, robotic solutions provide consistent, high-quality welds, reduce material waste, and improve safety by minimizing human exposure to hazardous conditions. Thus, they boost production rates and help manufacturers maintain the precision needed for large-scale, continuous operations.
The Advantages of Comau
Robotic Arc Welding Solutions
With a broad portfolio of MIG/MAG robotic welding systems, Comau offers complete, tailored solutions for any industrial need. Our welding robots are equipped with advanced features like adaptive welding, multipass capabilities, and real-time seam tracking to deliver superior performance in every application.
Comau offers customers expert guidance and the most effective robotic systems tailored to their specific industrial processes. Customers can also leverage Comau’s expertise by conducting welding tests with the support of our qualified specialists.
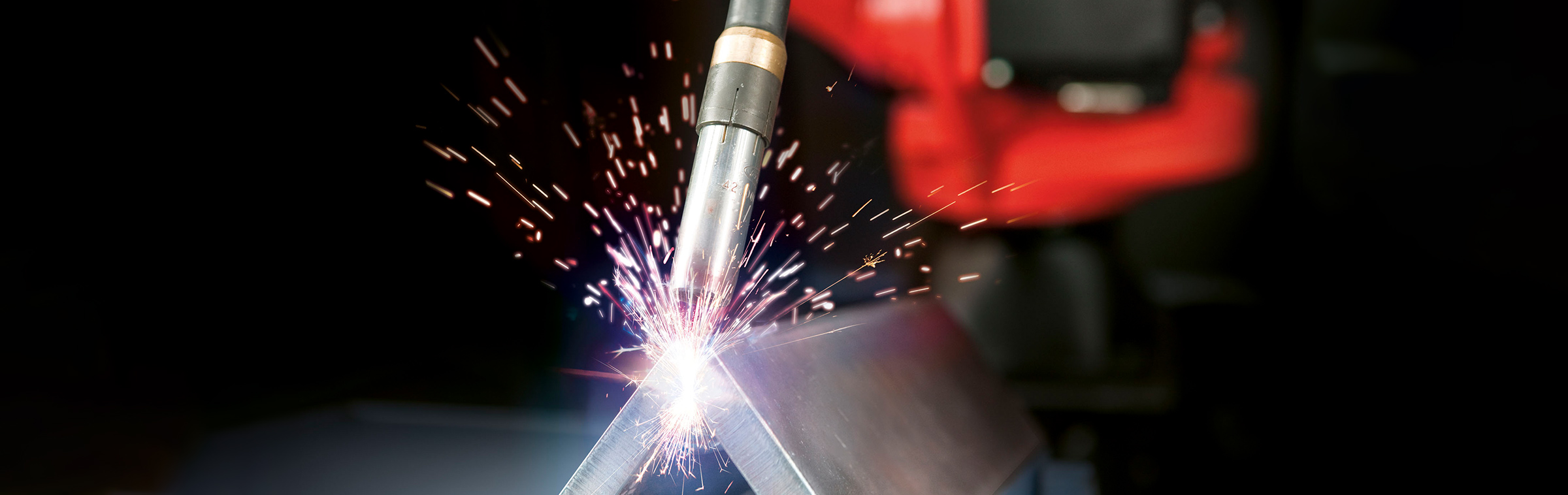
Automatic
Arc Welding
Application
Get insights from our tech expert, Gioacchino Civilettit on how to boost manufacturing efficiency through robotic welding
Want to know how Comau Robotic Arc Welding Solutions can boost manufacturing efficiency?
Do you need
more information?
Would you like to have
customized solution?
One supplier: Multiple Configurations
A complete Arc Welding set for any kind of industry
Strategic partnerships for power source, torch cleaning and lubricating
Our robots work with
Customizable, Turnkey Arc Welding Systems
Comau provides a complete range of automated arc welding solutions, from power sources to modular standard cells. Our robotic systems are designed for flexibility, allowing manufacturers to choose configurations that best fit their production lines. By leveraging strategic partnerships with leading suppliers, Comau ensures that your system is equipped with the latest technology for optimal performance.
Backed by decades of expertise in the automation and welding sectors, Comau’s solutions not only address the current gaps in manual welding but also set the stage for future-proof manufacturing. To optimize your welding operations and enhance productivity, contact Comau today for a customized robotic welding solution tailored to your needs.
Software Features for Arc Welding Applications
Smart Arc User Device
Application in the case of an alternative power source to Fronius
Multipass
Multiple welding seams with automatic shifts
Weaving
Allows for filling a wide, flat joint or welding thick metals by adding a weave pattern to cover a larger surface area
Adaptive Welding (Coming Soon)
Self-setting weaving amplitude and weld speed proportionally to the gap/ volume of the joint
Smart Arc Overlap
In case of welding interruption the robot will restart several millimeters back (value configurable)
Smart Arc Spot (Intermittent welding)
Welding with alternate Arc on and Arc off with the robot always in motion
Smart Arc Scratch start effect
Scratch the arc by scratching the wire, useful for oxidized parts
Automatic TPC – Check
Automatic control of torch tool value
Override
Changes welding parameters in real time
Multi- Arm cooperative
Two arms welding simultaneously on a rotating axis
Smart Search – Wire seam finder
Search joint using welding wire
Smart Arc Servo Robot Seam finder (Coming Soon)
Joint search using the laser Servo Robot sensor
Automatic stick-out calibration
Sets the wire stick-out in automatic mode
Wire seam tracker
Real-time tracking just ahead of where the weld is being deposited
SmartArcMoni (process monitoring)
Control of welding seam parameters