The growing global demand for low emission vehicles is driving Geely Automobile Holdings to adopt increasingly innovative production strategies tailored to the specific needs of electric and hybrid vehicle manufacturing. To meet this objective, the Geely Group needed to ramp-up production of its high-quality electric drive components. It turned to Comau for help, asking the industrial automation expert to develop and deploy a new e-drive assembly line that would guarantee high-speed, end-to-end production of the electric motor, gearbox and inverter at its Geely Vremt plant. The project would require Comau to increase Geely’s automation rate from 40% to 80% while maintaining best-in-class manufacturing standards, even at a full-scale production capacity of 120,000 jobs per year.
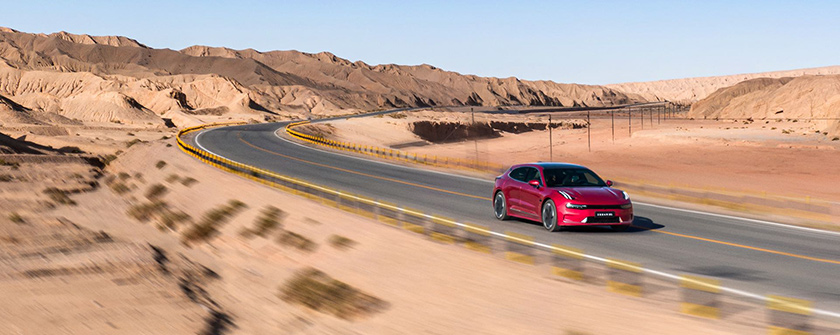
“Our goal of expanding productivity without sacrificing the trusted reliability that makes the Zeekr brand successful around the world was clear from the onset,” emphasized Sun Yongjing, Vice President of Geely Vremt. “Thanks to the close collaboration with Comau, we have experienced a significant increase in the agility and efficiency of our manufacturing processes. Furthermore, the innovative and highly automated assembly solutions have enabled us to double our current capacity while ensuring the exceptional quality our customers have come to expect.”
Sun Yongjing, Vice President of Geely Vremt.
The Challenge
Geely Vremt challenged Comau to design a high-speed e-drive assembly solution that would automate the complete, end-to-end production of electric motors, gearboxes and inverters. Geely also wanted to increase the plant’s overall level of automatization and improve workflow efficiency. Finally, the solution would need to uphold the customer’s rigorous quality parameters even at a target production capacity of over 100,000 jobs per year. Due to the high level of complexity, Comau and Geely engineers worked in close synergy during the entire project. Leveraging its extensive experience in powertrain assembly, Comau combined best-in-class technologies and engineering innovation to satisfy the customer’s high-volume production targets. The joint engineering team also faced unique technical and process challenges, including optimization of the magnetic block insertion and rotor injection activities, in addition to various automation issues related to high-speed loading, assembly and test phases.
The Solution
Assembly of the permanent magnet motor rotors has been achieved using multiple robots, automatic magnetization, detection, and dedicated production process solutions. The line features 3D vision positioning and guidance, automated high-speed magnet installation, automatic injection of rotor cores and the automatic dual-position dynamic balance correction, magnetization and more. To automate the gearbox production line, Comau used a Bosch TS2 conveyer, a flexible production system and multiple robots to perform automatic destacking in addition to other key processes. The online gear meshing test, Kistler servo pressing, shaft assembly and boxing technology have also been fully automated. In fact, the automation and process innovation levels seen in the line are arguably among the best in the e-drive gearbox industry. The final part of the solution automates the electric drive assembly and is based on a roller tray setup. The complete line includes advanced three-in-one assembly for motor stator casing, thermal sleeves, motor static testing, motor dynamic testing, automatic bearing feeding and pressing, automatic bolt feeding and tightening, and the automatic measurement and selection of gaskets. In addition to managing the complex technical intricacies of the project, the deployment team had to deal with supply challenges related to the COVID-19 pandemic, and post-delivery product optimization changes. Yet thanks to their quick and targeted response to these modification requests, mass production was officially launched in late 2021.
The Results
Comau has provided Geely with a powerful process solution that ensures higher quality and better throughput in less time. The successful delivery of this project also creates a concrete opportunity for Geely to capitalize on the growing interest in electric vehicles. Market research from IHS Markit indicates that electric vehicles could reach up to 80% of all new car sales by 2050. With its increased automation rate and expanded end-to-end production capabilities, the Geely Vremt plant is now ready to meet this level of global demand. More importantly, the automotive company can count on Comau’s ongoing support during the entire project lifecycle.
+
0-fold
increase in the plant’s automation rate
K
jobs per year production capacity
deg
high-speed, end-to-end assembly solution