SmartReach Comau ensures high-performance machining of large and complex lightweight aluminum parts
Designed to meet the evolving needs of lightweighting and electrification of automotive industry, aerospace, energy industries and other specialized sectors, SmartReach Comau combines the precision and stiffness of a machine tool, the agility of 5-axis continuous machining, and a unique modular and flexible structure for versatile solution configuration.
SmartReach Comau can easily be used in many machining application scenarios, increasing Overall Equipment Efficiency (OEE) while saving time, costs and energy consumption.
Overcoming Machining Gaps
Many manufacturing facilities struggle with integrating new technologies into existing processes. This includes the adoption of advanced machinery, IoT devices, and data analytics tools. SmartReach Comau bridges the gap between operational costs and quality control by combining high stiffness and repeatability maintaining consistent quality across the entire machining lines.
We build machines and develop complete machining processes to ensure productivity, flexibility and long-term reliable quality
In an environment often associated with high operational costs, such as energy consumption and maintenance, SmartReach Comau offers a low-energy machining alternative, also reducing floor space footprint with all maintenance at ground level.
High Precision Machining Solution
The cutting-edge solution was specifically created for machining of large and complex parts (e.g. AL mega casting underbodies, battery trays, aerospace structural components, etc.), offering unparalleled rigidity and stability.
Driven by a CNC controller and utilizing G-code, SmartReach Comau ensures precise and efficient operations. The machine system is equipped with fully integrated cables and hoses, enhancing its streamlined design. Additionally, SmartReach Comau features a high-performance spindle, making it an excellent choice for challenging machining tasks.
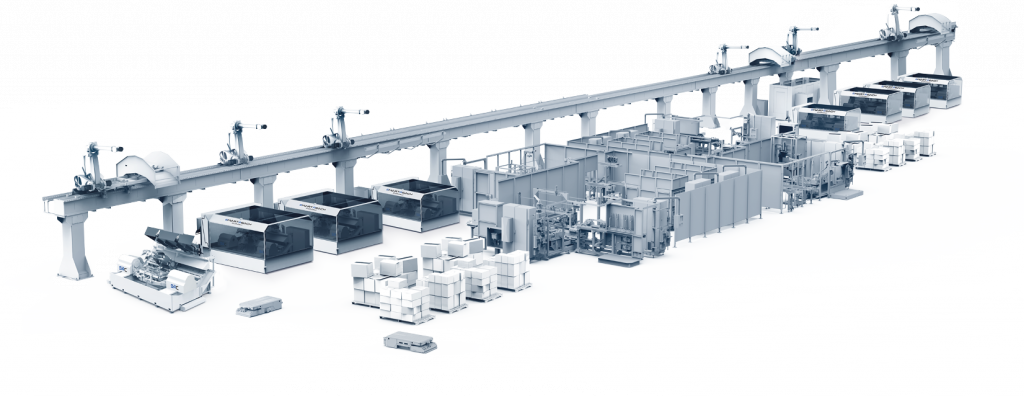
Key Features of SmartReach Comau
SmartReach Comau moves in a half-cylindrical envelope, moving around the part while performing 6-sided operations in one clamping position. With SmartReach Comau, there is no need to split operations between multiple stations, thus increasing overall productivity.
Alessandro Costa explains that SmartReach is engineered for high-speed, burr-free machining in hard-to-reach places.
- Real 5 axis continuous machining with CAD CAM and Programming G Code
- Six-sided agile machining in one clamping position
- Modular structure design, easy to reconfigure the most suitable solution for target part machining
- High flexibility and efficiency combined with high stiffness and high repeatability
- Compact footprint; low energy consumption
- Almost all maintenance at ground level
- Real time measuring during machining to reduce CT and scrappage rate
- Dry and MQL machining
- Full ESG compliance
Applications
Automotive
Lightweight Machining Parts
Multiple structural Aluminum components:
Battery trays
Mega casting underbodies
Shock absorbing tower
Front & rear cross beams and subframes
Aerospace
Full material machining
Complicated lightweight material structural parts which require flexible 5 axis continuous machining
With two SmartReach Comau devices working together, production is doubled
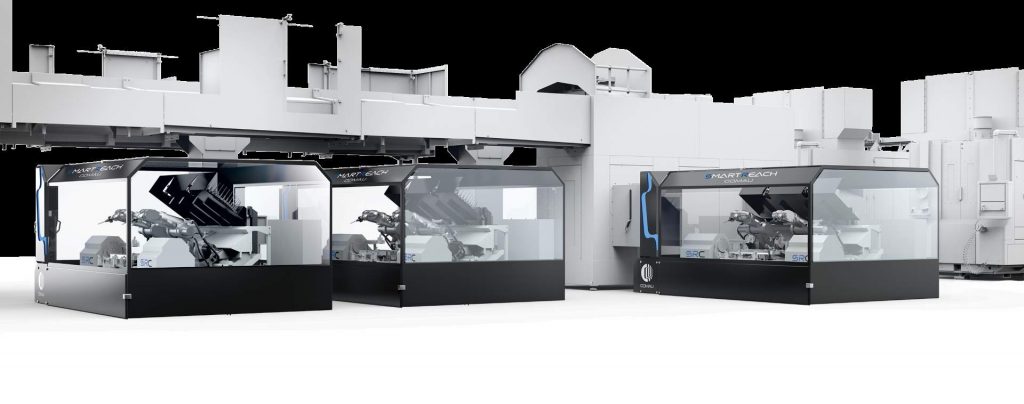
SmartReach Comau Twin grants the possibility to use two independent high-speed spindles on the same workpiece, or machine two workpieces together in the same machine, assuring high productivity and flexibility of the system.
One partner for the entire system
No matter how complex your machining needs are, our result-oriented methodology and systems expertise can support you. Comau has the competence to develop any machining process, assure productivity, flexibility and long-term quality that span the entire production chain, including assembly and test equipment across the lifetime of your manufacturing systems.
Automatic Loading
Comau supplies several configurations of carriages and arms to meet required production levels
Machining Centers
Comau machining centers are a perfect fit wherever maximum flexibility and productivity are non-negotiable
Want to know how SmartReach Comau fits your production Line?
more info
get a quote
Comau Machining Turnkey Capability at a glance
Comau’s turn-key competence in automation, ancillaries, assembly and test systems extends all the way to related digital solutions such as MES & IoT. We also have extensive retooling expertise, regardless of the machine brand, to help our customers protect the value of their existing lines. Finally, our additive knowhow includes PTWA thermal spray coating for emission reduction and performance enhancement.
Our spectrum ranges from single machining cells to complex systems with multiple integrated operations. Comau ensure productivity, long-term quality and continued reliability including a range of ancillaries such as:
- Tightening
- FSW
- Washing
- Final inspection
- Riveting
- Leak test
- Marking
- Logistics