Developing advanced technologies and manufacturing processes
With a successful track record in developing advanced technologies and manufacturing processes for the automotive sector, Comau Brazil has played a key role in the development of both the new Fiat Pulse, the brand’s first SUV model in Brazil and the Fiat Fastback, the brand’s first SUV Coupe and one of Fiat’s main launches in 2022 for the local market.
Comau was tasked with developing a high-volume, automated manufacturing line for the main body, the body sides and the respot operations for the two SUVs, both of which would need to be produced on the same assembly line. In response, Comau deployed its advanced body assembly solutions as part of a comprehensive retooling project at the Stellantis Automotive Plant in Betim – Minas Gerais.
“Beyond addressing the inherent automation challenges of the project, the Comau team was quick to propose and integrate key technologies to meet our quality and cycle-time objectives.This project, which is part of our Industry 4.0 strategy, has given us more agility and the flexibility to manufacture different versions and other models on the same lines.”
Glauber Fullana, Manufacturing Vice-president for Stellantis South America.
The Challenge
Stellantis challenged Comau to design a cutting-edge solution that would allow the company to meet its production targets, quality objectives and cycle times, using a pre-existing platform with enough flexibility to handle the unique size and specification variations of the two distinct SUV models.
Furthermore, Comau would need to retool and refurbish both the mainline and respot lines, to ensure large-scale, cost-effective manufacturing of multiple model variations while guaranteeing production continuity for the cars and passenger trucks the lines would be shared with. And with safety and flexibility as two essential pillars of the project, the assembly lines would also need to optimize automation efficiency with minimal line interventions.
Finally, in addition to managing the complex technical intricacies of the project, the Comau team found themselves dealing with a six-month standstill when the project was stopped due to the COVID-19 pandemic.
The Solution
Backed by a solid set of skills derived from decades of experience with the customer, Comau leveraged its local presence and technical know-how in diverse engineering fields to meet the demanding requirements of the project. The first step involved working directly alongside the automaker to sustainably retool and refurbish a total of 74 automatic and 10 manual stations for the SUV mainline, body sides and respot activities.
More specifically, the engineering team integrated Comau’s high-speed industrial robots with advanced vision systems, 3D adhesive dispensing, digital applications and turn-key equipment to create 3 main activity stations: the mainline manufacturing system (32 automatic and 2 manual stations); an additional 28 automatic stations and 6 manual loading lines for the body sides assembly line; and the respot assembly line (14 automatic and 2 manual stations). The comprehensive manufacturing solution also features Comau’s OpenGate system, which ensures geometrical accuracy while granting the inherent flexibility to handle multiple model configurations and an aggressive 52-second average cycle time.
To optimize the design and retooling of the complex lines, Comau utilized Virtual Commissioning capabilities and process simulation, allowing the team to test the expected performance and functionality prior to the onsite commissioning. In doing so, the team was able to anticipate eventual issues in terms of robot sequencing and the communication between the robots and PLC. Having a comprehensive view of the virtual plant also enabled Comau and Stellantis engineers to identify improvement points, enhance process monitoring and make better use of the legacy plant equipment, as well as optimizing intralogistics between the stations and lines. Combined, all of these features are essential aspects for an effective design-to-cost approach.
Another important highlight is the use of IO-Link technology to monitor the water and compressed air supply system, ensuring real-time analysis and agile problem detection. The integration of PLC software also contributes to optimizing maintenance activities, and the possibility of backing up robot activities via the corporate network ensures long-term reliability across the entire line.
The Results
As a result of the joint work by Comau and Stellantis, the remodeled lines allowed Stellantis to batch assemble 5 variants of its new Pulse SUV, among which the Pulse Abarth, and 2 variations of the Fastback SUV, including the Fastback Abarth model, all while sharing the assembly stations with other Fiat models.
Meeting the sustainability objective of reutilizing as much as possible from the original platform, Comau added 17 new robots and 45 new welding guns which together handle a total of up to 1000 welding spots for the SUVs’ body and bodysides. The solution also minimizes tool changes and line interventions, saving time and positively impacting the overall sustainability of the project.
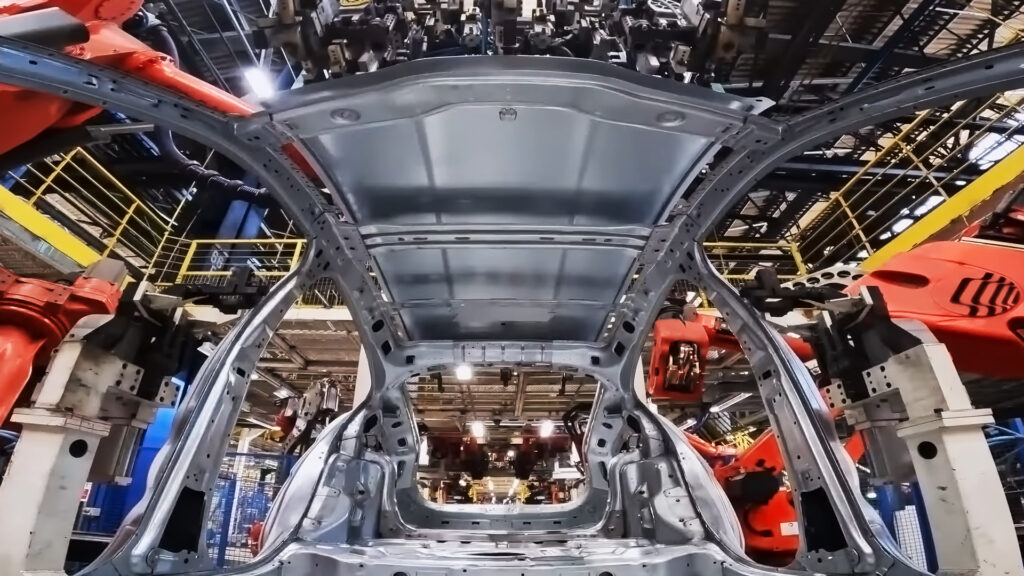
Comau’s in-depth process knowledge and its full integration with the customer’s engineering team allowed them to effectively deliver the project efficiently and on time. Having signed off on expected delivery milestones in October 2019, the team was forced to stop work for 6 months during the height of the global health pandemic. Yet because the Pulse and Fastback would be produced in tandem with other Fiat models on shared lines, the original launch date could not be altered. Thanks to Comau’s creativity, commitment and its use of Virtual Commissioning and process simulation, the team was able to optimize onsite delivery targets despite the unexpected project stop.
The innovative solution was developed by Comau Brazil with engineering support from Comau Romania, whose advanced vision system technologies ensure the aesthetic geometry precision and welding accuracy Stellantis required. Furthermore, the solution provides the customer with improved equipment efficiency and the flexibility to evolve from batch to random mix production in the future, as needed. Indeed, the project testifies to Comau’s ongoing commitment to both providing advanced manufacturing solutions and contributing to the development of quality vehicles for the Brazilian automotive industry.
automatic stations across three main lines
manual stations
welding spots per car body