The goal for the future is emission-free mobility. This requires technology suppliers to produce cutting-edge and sustainable battery and e-drive systems in an increasingly efficient way. Leading European companies, such as Comau, are particularly committed to this objective, with the global industrial automation company carrying out numerous innovative projects around the world in the field of electrification.
The Energy transition in the transport sector is becoming a reality. In line with the EU decarbonization objectives, the European Commission has adopted a package of legislative proposals “Fit for 55”, with which it aims to reduce greenhouse gas emissions from vehicles by 55% by 2030 and 100% by 2050. Electrification therefore represents the future of mobility. This means that encouraging more efficient and sustainable production of batteries and electric motors is clearly one of the most important challenges for companies working within the automotive and transportation industries. Among these, Comau plays a leading role. The Stellantis group subsidiary has gained consolidated experience in the automotive sector and is applying this know-how to related sectors that benefit from innovative automation solutions. Comau has its headquarters in Turin and operates in 13 countries around the world, with 6 innovation centers, 5 digital hubs and 9 factories, employing a total of 4,000 people.
Advanced solutions for battery manufacturing
The technological options for powering cars based on the use of lithium-ion batteries are constantly evolving. The market is characterized by extreme fluctuations, leading car manufacturers to demand flexible production solutions for cells, modules and different battery types. Both in EU-funded projects and for customers across Europe, Asia and the USA, Comau is active in consulting, designing and providing production and assembly systems for battery modules and packs with prismatic, cylindrical and pouch cells, both at a prototype level and for large-scale production. Innovation, sustainability and efficiency always play a central role, as can be seen at Leclanché, a Swiss manufacturer of lithium-ion cells and energy storage systems.
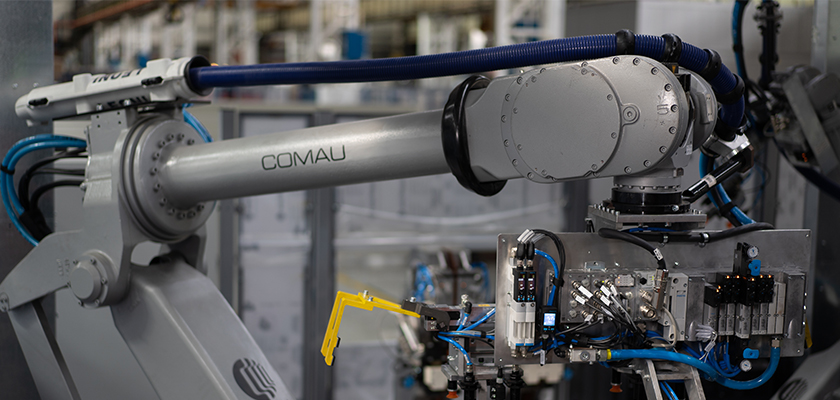
Comau has developed an automated production line to make lithium-ion battery modules for the naval sector, allowing Leclanché to increase its work capacity sixfold, automate complex manual processes and reduce operating costs by up to 20%. Trying to anticipate the technological trends that will guide the world of electrification, and thanks to its propensity for innovation and experimentation with cutting-edge solutions, Comau is collaborating with battery manufacturers, technology developers and international research centers for the industrialization of new generation cell production processes. In particular, through the supply of plants and with its engineering consultancy services, Comau is working with Ilika, a company specialized in the production of solid-state batteries, to increase the production capacity of its laboratory in the UK. The project plans to enhance the capacity from 1kWh to 10kWh per week, with the goal of helping the company move from prototyping to mass production.
From batteries to EV drive systems
Comau is also involved in important projects regarding the development of transmission systems for electric and hybrid cars, such as the project with Geely Automobile Holdings in China. Comau has designed and implemented an automated e-drive assembly line that is integrated into the company’s plant in Ningbo, China. The line is based on an automated and flexible system that allows the assembly of permanent magnet rotors, gearboxes and electric transmissions, in addition to managing quality control and automated tests of the final product. This innovative solution has allowed Geely to increase the automation rate of the plant from 40% to 80%, while achieving an impressive work capacity of 120,000 units per year. With great commitment, Comau is actively involved in important international collaborations for the design, construction and installation of production lines for electric motors and transmissions, as well as the assembly of stators – ranging from small series to full-scale industrial production, to get closer to the goal of zero emission mobility one step at a time.
Technologies for the mobility of the future
Comau collaborates with the world’s leading automotive manufacturers, supporting them in the creation of effective and flexible production processes, while at the same time providing innovative technologies for traditional, hybrid and electric vehicles. At its headquarters in Grugliasco (Turin), Comau has created an innovative Laser Lab to support companies in the design, implementation and optimization of laser processes for electric battery assembly applications.
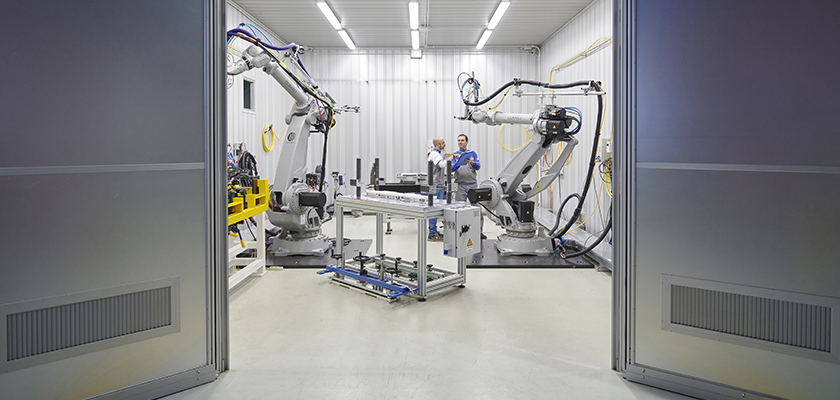
To date, more than 200 electric battery prototypes have been assembled inside it. Thanks to the technology center, Comau is able to help companies increase the capacity, speed and value of their production, supporting them in offering increasingly competitive solutions in the field of electrification. Comau also hosts the Battery Cell Global Competence Center at its headquarters, which is intended for the study and development of innovative systems and technologies for the mass production of cells. Here, direct support is provided to customers for the definition and optimization of the work process. In addition to the latter, there is an e-Motors Competence Center and a Battery Competence Center (for battery packs and modules), which today allow the company to cover the entire production chain of an electric car with specific and dedicated teams. For some time now, Comau has also been a partner of the Mirafiori Battery Lab. Thanks to the company’s expertise in assembly processes, it is supporting Stellantis in co-design activities and through the supply of production systems in the plant.
The added value of the network
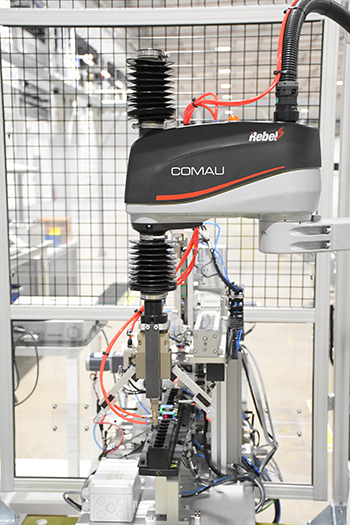
Comau has joined three major international consortia – the European Battery Alliance, the Batteries European Partnership Association and the European Technology and Innovation Platform – to promote the expansion of Europe’s battery sector.
Comau also collaborates with the UK Battery Industrialization Center (UKBIC) to design and implement a semi-automatic line for the assembly of battery modules and battery packs, which will aim to expand and strengthen the UK electrification market. Comau has provided all the technology and know-how necessary to manage the entire manufacturing process of the modules and battery packs, from the preparation of the cylindrical cells and the stacking of the pouch cells to the assembly of the battery pack. Comau’s know-how in the production and installation of photovoltaic systems and wind turbines has allowed it to collaborate with the WindEurope association to encourage the use of these technologies. Together with these activities in favor of renewable energy sources, Comau is experimenting with automation solutions in the hydrogen sector.
Promoting a sustainable transition
For energy transition to be truly sustainable, it is necessary to both efficiently produce cutting-edge technologies for electrification, and to manage the end-of-line environmental impact associated with the batteries themselves. This is why Comau has joined the “Battery regeneration project” promoted by the non-profit organization Class, and Cobat, a service platform for the circular economy. The project aims to promote an Italian supply chain for the recycling and reuse of lithium batteries. Internally, Comau, together with other electrification companies, research bodies, universities and institutions, is committed to identifying solutions for the reuse of vehicle batteries, helping to fuel the construction of a sustainable and circular value chain. As part of the initiative, Comau is involved in the development of automated solutions for the disassembly and re-assembly of battery packs and modules in compliance with safety standards. The company also provides its support through design activities for new battery packs.
Developing future-based skills
To be able to accommodate the needs of a constantly evolving market in the field of electrification, Comau has embarked on an important path of upskilling and reskilling of its internal resources as part of a project organized through the involvement of its Academy.
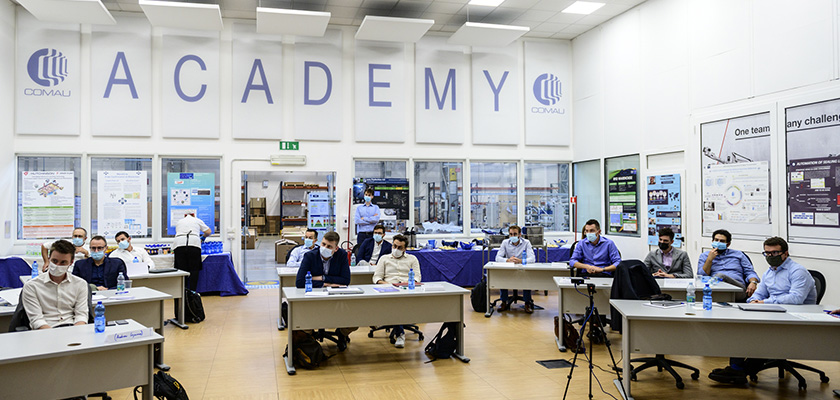
The goal is to improve and strengthen the skills of selected internal teams, through a training course specifically designed to respond to the various challenges that customers will face in the electric mobility sector in the future. The E-Skill program, which started in autumn 2021 and is now nearing completion of its second edition, has provided over 18,500 hours of training. Delivered both face-to-face and online, the program has involved an audience of more than 700 Comau employees – including new hires, staff, managers, workers and technicians.