When Jeep was preparing the factory for production of its new SUV, in one of the most modern automotive manufacturing plants in the state of Pernambuco, the conditions were clear and direct. Comau would be responsible for expanding the bodywork assembly systems to enable the car maker to produce their new 7 seat SUV Jeep Commander using a flexible method of production, fully alternated with 3 other models already fabricated, guaranteeing the same productive capacity of 48 vehicles per hour, which may also be expanded in the future. To increase the industrial park, Comau added 24 new robots, 24 welding pincers and 4 conveyor belts to the more than 620 assembly and welding robots already installed at the Jeep automotive factory in Goiana. Furthermore, the interventions in the 14 production lines projected by Comau, combining automatic, semi-automatic and manual operations, were made during the natural period of inactivity of the plant to guarantee the minimum impact on production.
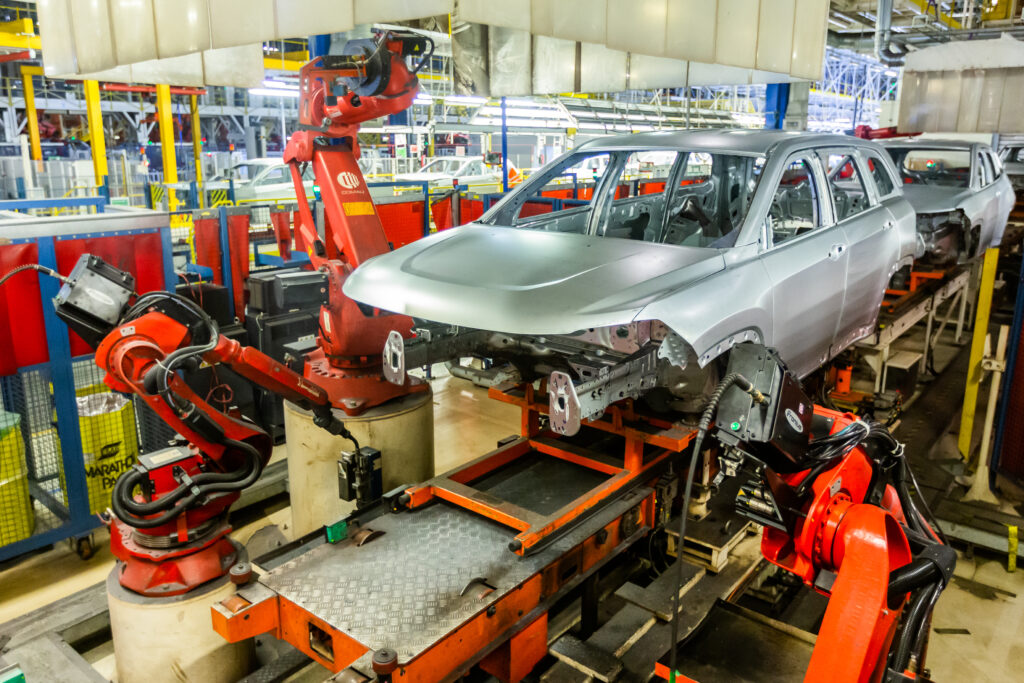
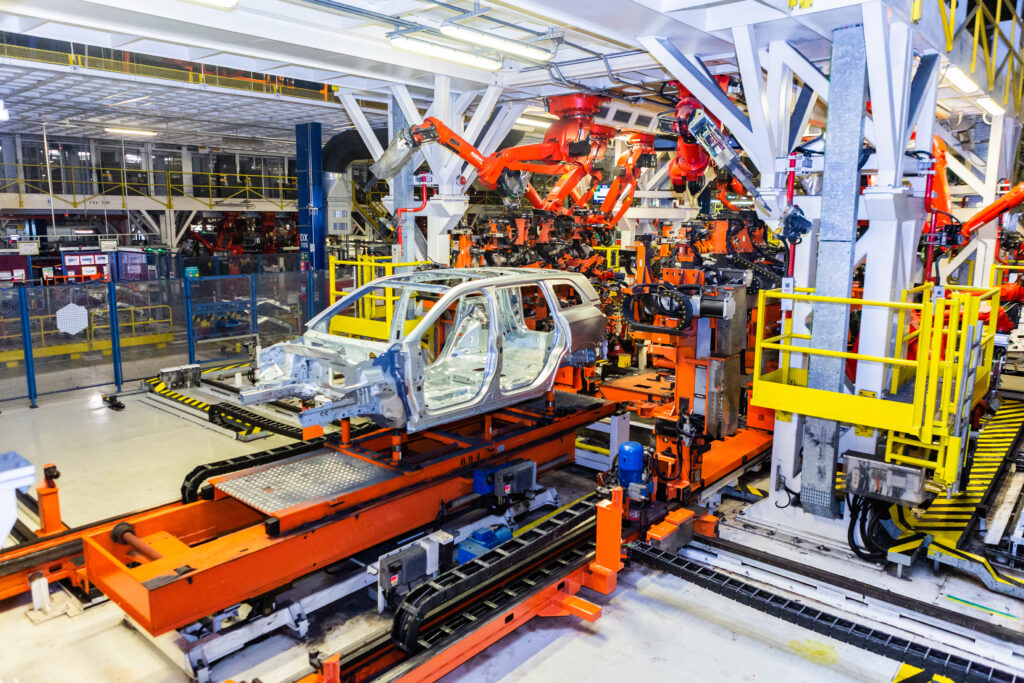
“From the start of the project, Comau have demonstrated their technical competence, expertise in automation and commitment to our success”, said Mateus Marchioro, Manager of the Jeep plant. “Despite the halting of the factory for almost 2 months, due to the COVID-19 pandemic, the team was able to conclude all the phases of the project ahead of schedule. Most important of all, the solutions proposed require less auxiliary equipment and less manual processing than we expected initially. We are pleased with the general performance of the new lines.
Mateus Marchioro, Manager of the Jeep plant
Die Herausfoderung
Jeep challenged Comau to design an innovative solution that would enable the car maker to produce their newest SUV on the same production lines that had been producing 3 of the top selling vehicles in Brazil, without sacrificing production or the cycle times. Improving the level of automation and improving the efficiency of the process was a further challenge, as the tooling changes needed from one model to another could generate inefficiencies if they were not designed carefully. Lastly, the lines would need to have inherent flexibility to allow Jeep to introduce new models in the future.
Comau’s technical know-how and the complete integration with the Jeep engineering team guaranteed the car maker had a project that was well done and completed on schedule. After mapping out the real production cycles, the Comau engineers worked with simulation tools to obtain a more complete picture of the modifications proposed to the layout of the assembly line before any implementation. The precise diagnosis of where and how the equipment and resources were being used guaranteed that all the modifications had been represented in a digital scenario, regardless of their origin. This allowed the team to optimize the commissioning in the plant and to reduce the downtime related to the implementation to a minimum. The team also used virtual commissioning to program the simulation of processes to speed up the implementation of the lines.
Die Lösung
To meet Jeep’s needs in relation to the flexibility of models, the Comau engineers had to expand the capacity of the innovative Butterfly system from 3 models to 4 models, with the random mix order of production. It was the first time the system would handle 4 models of different vehicles, which is designed in essence to plan the physical space for new equipment and robots when new models are introduced. At one point of the line, 14 robots apply 100 welding points in 52 seconds simultaneously to join the sides and the chassis in a single operation, guaranteeing a perfect geometry to the bodywork. At another stage, 70 robots apply structural adhesive to provide greater rigidity and resistance to infiltration of dust and water. In total, each vehicle receives more than 3,000 welding points during the assembly process.
Other modifications to the line include the improvement of the Comau automatic welding and assembly system, VersaRoll. In doing this, the engineering team eliminated the need for calibration of the device and optimized the number of robots per station. Similarly, the Tool Tray Shuttle was expanded to operate with 4 tables for the first time and thus be better adapted to the specific assembly needs of the new SUV.
To face the challenges related to the pandemic, which included the impossibility of accessing the plant during the period of mandatory closure, Comau do Brasil adopted a fluid project management approach. The team worked remotely in Smart Working, making use of simulation projects of cells and virtual commissioning tools before moving to a gradual and safe return of activities in the factory. The team also had to manage delays in the delivery of components and was able to do this concentrating on the parts of the project for which the supplies were available on time. As a result, Comau was able to bring forward the schedule, implementing Project 598 in less than 24 months, from start to finish. More importantly, this was done without compromising the flow or the natural volumes of production of the Jeep plant in Goiana.
Das Ergebnis
With a lean manufacturing approach, the innovative Comau solution has a high proportion of advanced automation processes, as well as involving less auxiliary equipment. Cameras are used to detect parts by shape, instead of sensors and photocells. The complete 3D digitalization of the line stations guaranteed perfect robotic alignment. Proprietary Comau solutions were also implemented, such as laser welding, viewing and the clipping Roller Hemming – RHEvo systems. Besides this, the configuration compatible with Industry 4.0 uses the IO-link technology to help monitor important processes, such as the water and compressed air systems and helps to detect any problems very quickly and effectively. All this affords Jeep high efficiency of the equipment and the improvement in quality inspection resources.
To help protect the scalability of the client’s investments, the whole project was developed to allow Jeep to introduce new models in the future. Furthermore, the project led by Brazil represents the global capacity of Comau to respond to complex challenges to the highest fabrication standards, with the direct collaboration of professionals at Comau Romania, Comau Italy and Comau China. Thus, Comau do Brasil was able to leverage their local presence and technical expertise over a long time in automation, digitalization and intelligent technologies to deliver speed, quality and efficiency on which Jeep can rely to produce their premium vehicles.
To help protect the scalability of the customer’s investment, the entire project was designed to enable Jeep to introduce new models in the future for a fraction of the initial expenditure. Furthermore, the Brazilian-led project represents Comau’s global capacity to respond to complex challenges while meeting the highest manufacturing standards, benefiting from direct support from Comau Romania, Comau Italy and Comau China. As such, Comau Brazil was able to leverage its local presence and longstanding expertise in automation, digitalization and intelligent technologies to deliver the speed, quality and efficiency Jeep can rely on to produce its premium vehicles.
models of vehicles assembled in a complex of 14 lines with random order of production
+
Comau robots installed
welding points applied every 52 seconds
loss of productivity during the expansion process