Have you ever wondered if a high-speed industrial robot could clean and manipulate high-end cosmetic bottles without leaving a single mark? This was the challenge Cosmint faced in response to an increased production demand by one of the premium cosmetic and skincare brands they serve. Working with some of the world’s biggest names in cosmetics, Cosmint is known for its high-quality standards and advanced technology. This is why the Italian manufacturer asked Siscodata, a System Integrator with whom they had previously worked on various robotic projects, to design an innovative depalletizing solution able to pick, clean, rotate and deliver custom-printed plastic bottles at an accelerated rate of 150 pieces per minute.
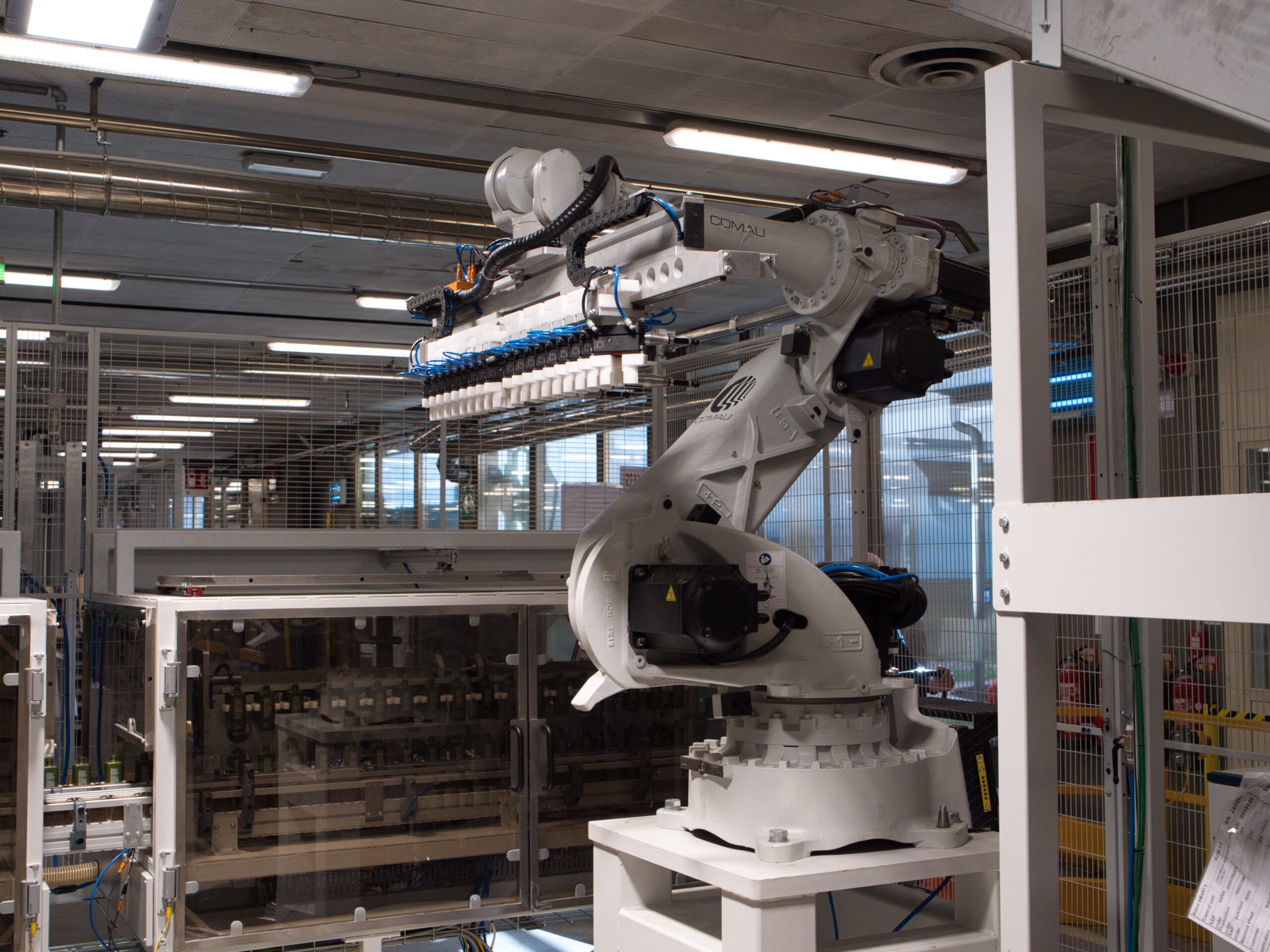
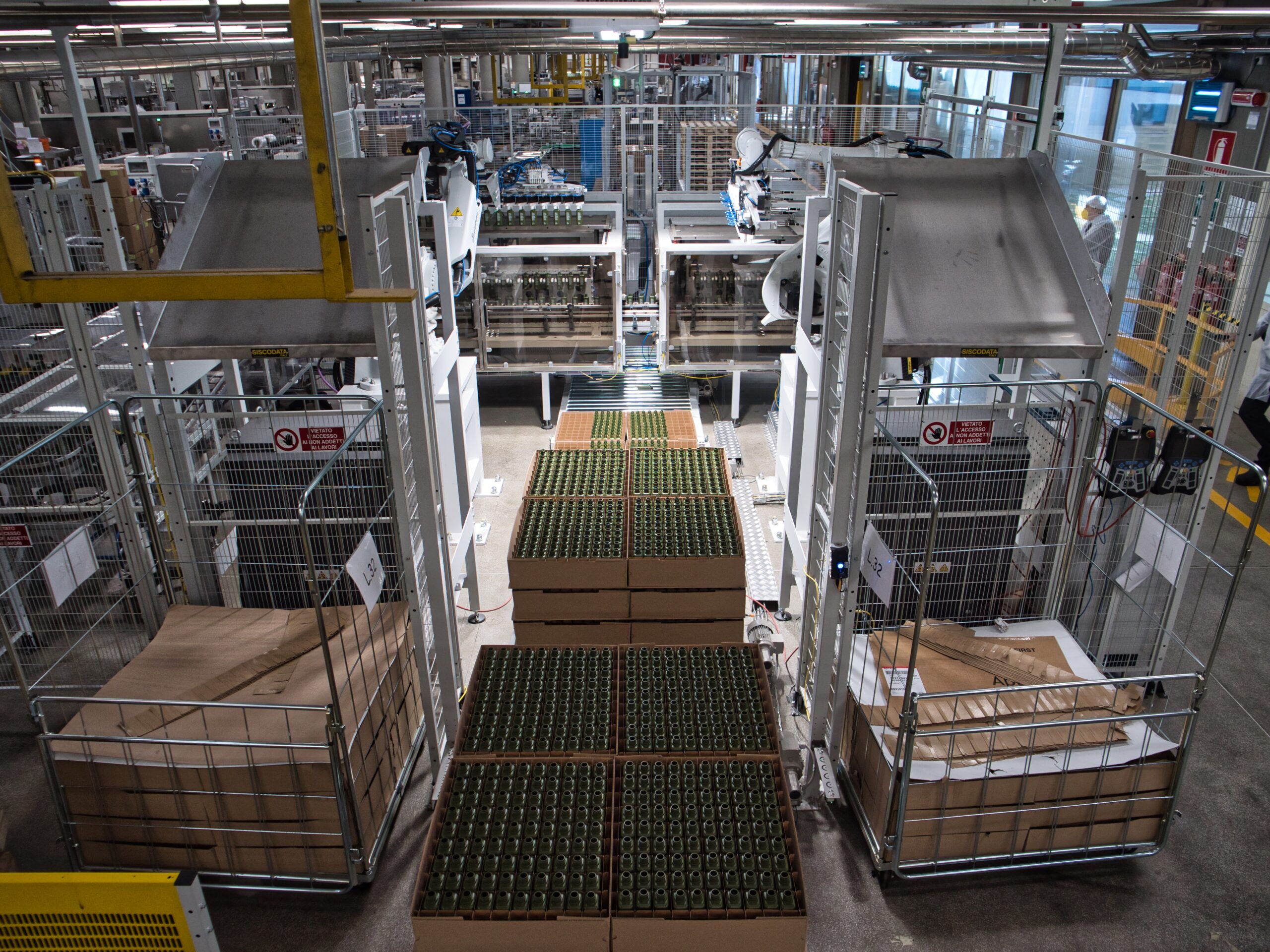
“We asked Siscodata to develop a single cell that would both replace three standard machines and expand our productivity. In only four and a half months from start to finish, they did it,” explained Francesca Grieco, Engineering Manager at Cosmint Spa. “We are particularly satisfied with the Comau robots, which have allowed us to reach our target of creating a system that is 100% reliable from a performance, quality and electro-mechanical standpoint, and can guarantee the exceptionally high cleanliness standards specified by our end customer.”
Francesca Grieco, Engineering Manager at Cosmint Spa
Die Herausfoderung
In addition to the sheer complexity of the automation itself, Cosmint challenged Siscodata to design a high-speed solution that would virtually eliminate residue contamination while respecting the delicate nature of the premium containers. Cosmint also required a production rate of up to 150 bottles per minute, which translates to less than 0.45 seconds per bottle.
Another difficulty was dealing with the reduced space when picking the bottles from the honeycomb cardboard. The Siscodata team also needed to create a gripper that could adapt to the differences in distances between the incoming boxes and the captive plate pucks leading to the washing system. Finally, the solution would need to uphold the rigorous quality and cleanliness parameters set forth by the final customer in order to pass their URS (User Requirements Specifications) Tests.
Die Lösung
Working side-by-side the Cosmint Technology Transfer team, Siscodata created an automated depalletizing solution using two Comau NJ-40 articulated robots that would guarantee the speed, precision and repeatability the application required. The team chose Comau both because their robots were already installed in other Cosmint cells and because Siscodata has worked with Comau on projects around the world for more than 20 years.
The solution starts with the arrival of custom-printed, 150x40x53 mm bottles, which have been shipped by truck in fragile, honeycombed carton containers. With the use of a high-resolution illumination camera to guide the robots, a series of 18 bottles are picked from the honeycomb containers and moved to the adjacent cleaning station. Due to the height of the pallet, the vision system initially had optical lighting difficulties and parallax tolerances between the top of the pallet and the bottom of the wood despite its very high resolution 2D camera and the pallet cardboard slant. To address this issue, the team modified the grid calibration of the camera. Instead of its typical single calibration, the camera has been modified to have a different grid-memorized calibration for each specific level, allowing the robot to manage the camera based on which part of the pallet it is working on.
Indeed, the Comau robot first goes to database and changes the camera’s calibration set-up based on the pallet level from which it needs to pick the bottles, allowing the two robots to work in tandem at very fast speeds. Furthermore, each robot has been fitted with self-adjusting grippers and auxiliary features expressly designed to minimize the risk of scratching the high-end bottles, which would affect the aesthetic and overall quality of the final product. These include scratch-proofing guides and velvet-covered gripper hands to avoid damaging the bottles, especially the Company logo.
After the bottles are depalletized, they are rotated 90 degrees so they are in the correct refilling position. Because Cosmint’s final customer has imposed extremely high cleanliness requirements, the bottles are moved to a double work station where the robots help remove residual particles or contaminants left over from the production, shipping and depalletizing processes. This part of the solution is quite complex and requires synchronized “on the fly” movements by the robots (150 pieces/minute means equates to 0.45 seconds per bottle, including the time needed to move the bottle). The team designed a system that first cleans each bottle with a flow of filtered air. Then, to be even more certain, the system uses an absolute filter and deionizers to eliminate any electrostatic charge before lingering dust and plastic particles are definitively suctioned out of the bottles.
The Results
Using Comau robots, Siscodata designed an innovative high-speed automated cell to replace three standard machines to expanding Cosmint’s productivity while protecting the high-quality standards the company is known for. Specifically created for pre-printed plastic cosmetic containers, the solution was developed in just 4 ½ months and installed in a single week. More importantly, it helps ensure that the end-customer receives a product that is free from contamination and 100% compliant to their rigorous standards.
The fully integrated solution has allowed Cosmint to successfully meet the requests of their client and achieve each of the goals they aspired to: protecting the aesthetic quality and purity of the final product, achieving a production rate of 150 bottles per minute and ensuring mechanical, electronic and electrical efficiency.
<
0%
residual contamination inside the container
≈
0risk of damaging or scratching the premium containers
k
bottles handled per hour
%
adaptable to different industries and payloads