Die weltweit steigende Nachfrage nach emissionsarmen Fahrzeugen zwingt Geely Automobile Holdings dazu, zunehmend innovative Produktionsstrategien zu entwickeln, die auf die spezifischen Anforderungen der Fertigung von Elektro- und Hybridfahrzeugen ausgerichtet sind. Um diese Zielsetzung zu erfüllen, musste die Geely Gruppe die Produktionskapazität ihrer hochwertigen Elektroantriebskomponenten steigern. Die Gruppe wandte sich an Comau, den Experten für industrielle Automatisierung, um eine neue E-Antriebsmontagestraße entwickeln und einrichten zu lassen, die eine schnelle End-to-End-Produktion des Elektromotors, Getriebes und Wechselrichters im Werk Geely Vremt ermöglicht. Im Rahmen dieses Projekts musste Comau die Automatisierungsrate von Geely von 40 % auf 80 % steigern und gleichzeitig die hohen Herstellungsstandards bei einer Produktion im industriellen Maßstab mit einer Kapazität von 120.000 Aufträgen pro Jahr aufrechterhalten.
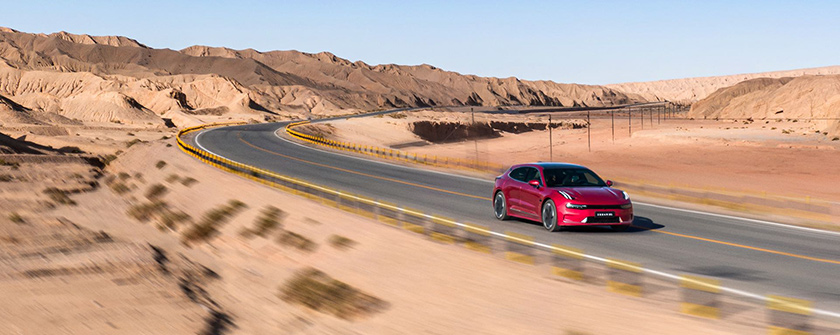
„Unser Ziel, die Produktivität zu steigern, ohne die Zuverlässigkeit in Frage zu stellen, die die Marke Zeekr weltweit so erfolgreich macht, stand von Anfang an im Vordergrund‘, erläutert Sun Yongjing, Vizepräsident von Geely Vremt. „Dank unserer engen Zusammenarbeit mit Comau konnten wir die Agilität und Effizienz unseres Herstellungsprozesses erheblich steigern. Darüber hinaus haben uns die innovativen und stark automatisierten Montagelösungen ermöglicht, unsere Produktionskapazität zu verdoppeln und gleichzeitig die außerordentliche Qualität, die unsere Kunden von uns erwarten, zu gewährleisten.“
Sun Yongjing, Vizepräsident von Geely Vremt
Die Herausfoderung
Geely Vremt hat Comau damit beauftragt, eine schnelle E-Antriebsmontagelösung zu entwickeln, die die komplette End-to-End-Produktion von Elektromotoren, Getrieben und Wechselrichtern automatisiert. Geely wollte auch das allgemeine Automatisierungsniveau seines Werks sowie die Effizienz der Arbeitsabläufe verbessern. Und schließlich sollte die Lösung die anspruchsvollen Qualitätsvorgaben des Kunden auch bei einer Zielproduktionskapazität von über 100.000 Aufträgen pro Jahr erfüllen.
Angesichts der besonderen Komplexität dieses Auftrags haben die Ingenieure von Comau und Geely während des gesamten Projekts eng zusammengearbeitet. Comau hat seine umfassende Erfahrung in der Montage von Antriebssträngen in Verbindung mit hochmodernen Technologien und innovativen Konstruktionslösungen eingebracht, um die Anforderungen an die hohen Produktionsziele des Kunden zu erfüllen. Das gemeinsame Konstruktionsteam sah sich auch mit einmaligen technischen und prozessrelevanten Herausforderungen konfrontiert, darunter der optimierte Einbau des Magnetblocks sowie das Einpressen des Rotors und die zahlreichen Automatisierungsprobleme in Verbindung mit der schnellen Beladung und den Montage- und Testphasen.
Die Lösung
Die Montage der Rotoren des Permanentmagnetmotors wurde dank des Einsatzes verschiedener Roboter, einer automatischen Magnetisierung und Detektion sowie individueller Produktionsprozesslösungen möglich gemacht. Die Montagestraße zeichnet sich durch 3D-Positionierungs- und Führungssysteme, eine automatische Installation der Magneten mit hoher Geschwindigkeit, das automatische Einpressen der Rotorkerne, die automatische dynamische doppelte Unwuchtkorrektur, Magnetisierung und vieles mehr aus.
Zur Automatisierung der Getriebeproduktionsstraße nutzte Comau das Transfersystem TS2 von Bosch, ein flexibles Produktionssystem und mehrere Roboter für das automatische Abstapeln zusätzlich zu den anderen wichtigen Prozessen. Die Online-Getriebeprüfung, die Kistler Servo-Pressen, die Wellenmontage und die Verpackungstechnologie sind ebenfalls vollständig automatisiert worden. Der Innovationsgrad der Automatisierung und der Prozesse dieser Montagestraße gehört zweifellos zu den Besten in der E-Antriebsgetriebeindustrie.
Im letzten Teil der Lösung wird die Montage des Elektroantriebs basierend auf einem Roller-Tray automatisiert. Die komplette Montagestraße umfasst fortschrittliche 3-in-1-Montagesysteme für Statorgehäuse, Wärmeschutzhüllen, statische Motortests, dynamische Motortests, automatisches Zuführen und Einpressen von Lagern, automatisches Zuführen und Anziehen von Bolzen sowie die automatische Messung und Auswahl von Dichtungen.
Neben den vielen technischen Schwierigkeiten des Projekts musste das Deployment-Team auch die zahlreichen Herausforderungen in Bezug auf die COVID-19-Pandemie sowie die Änderungen zur Optimierung des Produkts nach der Lieferung meistern. Dank der schnellen und gezielten Antworten auf diese Änderungsanfragen nach der Lieferung konnte die Serienproduktion jedoch offiziell Ende 2021 gestartet werden.
Das Ergebnis
Comau hat Geely eine leistungsfähige Prozesslösung geliefert, die eine höhere Qualität und einen verbesserten Durchsatz in weniger Zeit gewährleistet. Die erfolgreiche Lieferung dieses Projekts stellt für Geely eine konkrete Gelegenheit dar, von dem wachsenden Interesse an Elektrofahrzeugen zu profitieren. Ein Marktforschungsbericht von IHS Markit ergibt, dass Elektrofahrzeuge bis 2050 einen Anteil von bis zu 80 % aller Neuwagenkäufe erreichen könnten. Dank der gesteigerten Automatisierungsrate und der verbesserten End-to-End-Produktionskapazitäten ist das Werk von Geely Vremt jetzt in der Lage, die globale Nachfrage auf diesem Niveau zu erfüllen. Noch wichtiger ist jedoch, dass der Automobilhersteller während gesamten Projektlaufzeit auf den kontinuierlichen Support von Comau zählen kann.
x
0Automatisierungsrate der Werks
k
Aufträgen jährlich
Grad
End-to-End-Montagelösung mit hoher Geschwindigkeit