Entwicklung fortschrittlicher Technologien und Fertigungsprozesse
Mit einer Erfolgsgeschichte bei der Entwicklung fortschrittlicher Technologien und Fertigungsprozesse für den Automobilsektor spielte Comau Brasilien eine Schlüsselrolle bei der Entwicklung des neuen Fiat Pulse, des ersten SUV-Modells der Marke in Brasilien, und auch des Fiat Fastback, des ersten SUV-Coupés der Marke und einer der wichtigsten Markteinführungen der Marke für den lokalen Markt im Jahr 2022.
Comau wurde mit der Entwicklung einer hochvolumigen, automatisierten Fertigungslinie für die Hauptkarosserie, die Karosserieseiten und die Ausschweißarbeiten für die beiden SUVs beauftragt, die beide auf derselben Montagelinie produziert werden müssen. Dafür setzte Comau seine fortschrittlichen Karosseriemontagelösungen im Rahmen eines umfassenden Retooling-Projekts in der Stellantis Automotive Plant in Betim – Minas Gerais ein.
„Neben der Bewältigung der Automatisierungsherausforderungen des Projekts war das Team von Comau in der Lage, schnell Schlüsseltechnologien vorzuschlagen und zu integrieren, um unsere Ziele hinsichtlich Qualität und Zykluszeit zu erreichen. Dieses Projekt, das Teil unserer Industrie-4.0-Strategie ist, hat uns mehr Agilität und die Flexibilität verschafft, verschiedene Versionen und andere Modelle auf denselben Linien zu fertigen.“
Glauber Fullana, Manufacturing Vice-President bei Stellantis South America
Die Herausfoderung
Stellantis stellte Comau vor die Herausforderung, eine hochmoderne Lösung zu entwickeln, die es dem Unternehmen ermöglichen würde, seine Produktionsziele, Qualitätsziele und Zykluszeiten zu erreichen. Zur Bewältigung der einzigartigen Größen- und Spezifikationsvarianten der beiden unterschiedlichen SUV-Modelle wurde eine bereits vorhandene Plattform mit ausreichender Flexibilität verwendet.
Darüber hinaus müsste Comau sowohl die Hauptlinie als auch die Ausschweißlinien umrüsten und modernisieren, um eine kosteneffektive Großserienfertigung mehrerer Modellvarianten zu gewährleisten und gleichzeitig die Produktionskontinuität für die Pkw und Personen-Lkw zu gewährleisten, mit denen die Linien gemeinsam genutzt würden. Und da Sicherheit und Flexibilität zwei wesentliche Säulen des Projekts sind, müssten die Montagelinien auch die Automatisierungseffizienz mit minimalen Eingriffen an der Linie optimieren.
Schließlich musste das Comau-Team nicht nur die komplexen technischen Feinheiten des Projekts bewältigen, sondern hatte auch mit einem sechsmonatigen Stillstand zu kämpfen, als das Projekt aufgrund der COVID-19-Pandemie gestoppt wurde.
Die Lösung
Gestützt auf eine Reihe solider Fähigkeiten, die auf jahrzehntelanger Erfahrung mit dem Kunden basieren, nutzte Comau seine lokale Präsenz und sein technisches Know-how in verschiedenen technischen Bereichen, um die anspruchsvollen Anforderungen des Projekts zu erfüllen. Der erste Schritt bestand darin, in direkter Zusammenarbeit mit dem Automobilhersteller insgesamt 74 automatische und 10 manuelle Stationen für die SUV-Hauptlinie, Karosserieseiten und Ausschweißarbeiten nachhaltig umzurüsten und zu modernisieren.
Genauer gesagt integrierte das Engineering-Team die Hochgeschwindigkeits-Industrieroboter von Comau mit fortschrittlichen Vision-Systemen, 3D-Klebstoffdosierung, digitalen Anwendungen und schlüsselfertiger Ausrüstung zur Realisierung von 3 Stationen für die Hauptaktivitäten: das Hauptlinien-Fertigungssystem (32 automatische und 2 manuelle Stationen), zusätzliche 28 automatische Stationen und 6 manuelle Beladelinien für die Karosserieseiten-Montagelinie und die Ausschweißmontagelinie (14 automatische und 2 manuelle Stationen). Die umfassende Fertigungslösung verfügt auch über das OpenGate-System von Comau, das geometrische Genauigkeit gewährleistet und gleichzeitig die inhärente Flexibilität bietet, mehrere Modellkonfigurationen und eine aggressive, durchschnittliche Zykluszeit von 52 Sekunden zu bewältigen.
Zur Optimierung des Designs und der Umgestaltung der komplexen Linien nutzte Comau die Funktionen für die virtuelle Inbetriebnahme und die Prozesssimulation, sodass das Team die erwartete Leistung und Funktionalität vor der Inbetriebnahme vor Ort testen konnte. Dabei konnte das Team eventuelle Probleme bei der Robotersequenzierung und Kommunikation zwischen Robotern und SPS voraussehen. Eine umfassende Sicht auf die virtuelle Anlage ermöglichte es den Ingenieuren von Comau und Stellantis auch, Verbesserungspunkte zu identifizieren, die Prozessüberwachung zu verbessern und die Ausrüstung der alten Anlage besser zu nutzen sowie die Intralogistik zwischen den Stationen und Linien zu optimieren. Zusammengenommen sind all diese Merkmale wesentliche Aspekte für einen effektiven Design-to-Cost-Ansatz.
Ein weiteres wichtiges Highlight ist der Einsatz der IO-Link-Technologie zur Überwachung des Wasser- und Druckluftzufuhrsystems, die eine Echtzeitanalyse und agile Problemerkennung zu gewährleistet. Die Integration von SPS-Software trägt auch zur Optimierung von Wartungsaktivitäten bei, und die Möglichkeit, Roboteraktivitäten über das Unternehmensnetzwerk zu sichern, gewährleistet langfristige Zuverlässigkeit über die gesamte Linie.
Das Ergebnis
Aufgrund der Zusammenarbeit von Comau und Stellantis konnte Stellantis mit den umgebauten Linien 5 Varianten seines neuen Pulse-SUV montieren, darunter den Pulse Abarth und 2 Varianten des Fastback-SUV, einschließlich des Fastback Abarth-Modells und all das, während die Montagestationen mit anderen Fiat-Modellen gemeinsam genutzt wurden.
Um das Nachhaltigkeitsziel zu erreichen, so viel wie möglich von der ursprünglichen Plattform zu nutzen, hat Comau 17 neue Roboter und 45 neue Schweißzangen hinzugefügt, die zusammen bis zu 1000 Schweißpunkte für die Karosserie und die Karosserieseiten der SUVs bewältigen. Die Lösung minimiert auch Werkzeugwechsel und Linieneingriffe, spart Zeit und wirkt sich positiv auf die Gesamtnachhaltigkeit des Projekts aus.
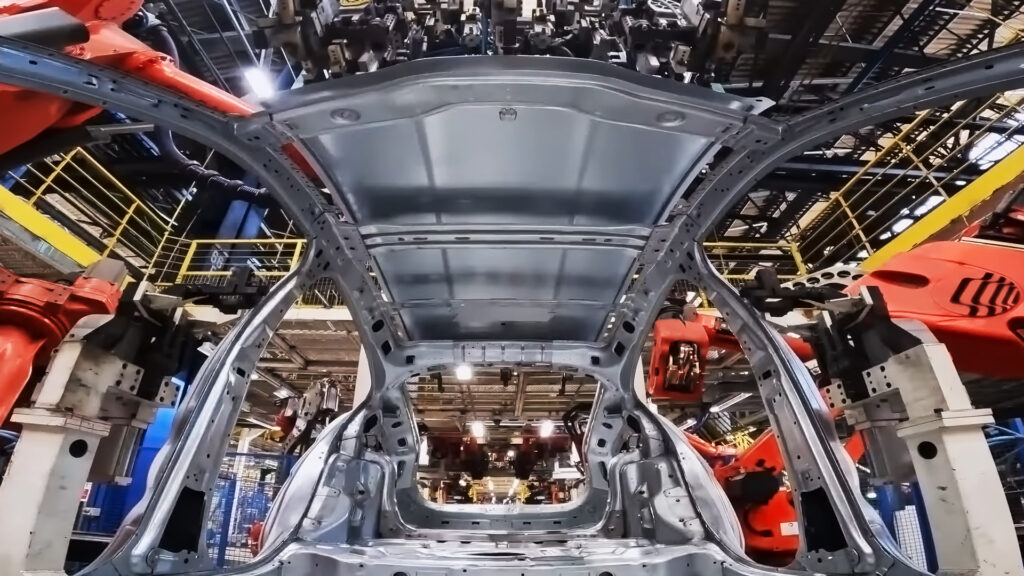
Dank des fundierten Prozesswissens von Comau und der vollständigen Integration in das Engineering-Team des Kunden konnte das Unternehmen das Projekt effizient und termingerecht umsetzen. Nachdem das Team im Oktober 2019 die erwarteten Liefermeilensteine abgezeichnet hatte, war es gezwungen, die Arbeit während des Höhepunkts der weltweiten Gesundheitspandemie sechs Monate lang einzustellen. Da der Pulse und Fastback jedoch zusammen mit anderen Fiat-Modellen auf gemeinsamen Linien produziert werden würden, konnte das ursprüngliche Einführungsdatum nicht geändert werden. Dank der Kreativität, des Engagements und des Einsatzes der virtuellen Inbetriebnahme und Prozesssimulation von Comau konnte das Team die Lieferziele vor Ort trotz des unerwarteten Projektstopps optimieren.
Die innovative Lösung wurde von Comau Brasilien mit technischer Unterstützung von Comau Rumänien entwickelt, deren fortschrittliche Vision-Systemtechnologien die von Stellantis geforderte ästhetische Geometriepräzision und Schweißgenauigkeit gewährleisten konnte. Darüber hinaus bietet die Lösung dem Kunden eine verbesserte Anlageneffizienz und die Flexibilität, sich in Zukunft je nach Bedarf von der Batch- zur Random-Mix-Fertigung zu entwickeln. In der Tat zeugt das Projekt von Comaus anhaltendem Engagement, fortschrittliche Fertigungslösungen anzubieten und auch zur Entwicklung von Qualitätsfahrzeugen für die brasilianische Automobilindustrie beizutragen.
automatische Stationen verteilt auf drei Hauptlinien
manuelle Stationen
Schweißpunkte pro Karosserie