Heute sind Aspekte wie „Kohlenstoff-Spitzenwert“ und „Kohlenstoffneutralität“ globale Zielsetzungen. China hat sich eindeutig dazu bekannt, seinen „Kohlenstoff-Spitzenwert bis 2030 und die Kohlenstoffneutralität bis 2060 zu erreichen“. Angesichts dieses langfristigen Ziels konzentrieren sich die großen Autohersteller darauf, Energieeinsparungen und Emissionsreduktionen so früh wie möglich zu erreichen, setzen aber auch auf die Entwicklung und Erforschung neuer Energiequellen und die Einführung effizienterer, umweltfreundlicherer und energieeffizienterer Motoren. 2018 brachte Nissan den weltweit ersten, in Serie gefertigten VC-Turbo-Motor auf den Markt – einen Motor mit variabler Verdichtung, der Motorleistung und Kraftstoffverbrauch in Einklang bringt. Der Autohersteller konnte durch eine lokale Produktion auch einen wettbewerbsfähigeren Preis auf dem chinesischen Markt anbieten.
„Unser Motorenmodell 2.0T umfasst sowohl einen 4-Zylinder-Reihenmotor mit variabler Verdichtung als auch einen 3-Zylinder-Reihenmotor mit variabler Verdichtung und Turboaufladung“, erläutert der Engine Technical Leader Chen Xiaosen von Dongfeng Nissan. „Aus strategischen Gründen haben wir uns dafür entschieden, die beiden Motorentypen auf einer gemeinsamen Linie zu produzieren. Das kollineare Produktionsverfahren stellt jedoch höhere Anforderungen an die Produktionslinie, nicht nur um eine automatische Verarbeitung zu erreichen, sondern auch um ein angemessenes Maß an Flexibilität zu gewährleisten.“
Engine Technical Leader Chen Xiaosen von Dongfeng Nissan
Die Herausfoderung
Im Januar 2019 wurde Comau von Dongfeng Nissan mit der Entwicklung und Implementierung eines automatisierten Hochgeschwindigkeits-Motorenmontagesystems beauftragt, das die Hauptlinien (Montagelinien für Zylinderkopf, Short Block, Kolbenstange, unbestückten Motor und vollständigen Motor) sowie nicht standardmäßige Bearbeitungsarbeitsplätze zur Zylinderkopfbearbeitung, Be- und Entladestationen für Roboter sowie entsprechende Ablagen umfasst.
Da es sich bei dem VC-Turbomotor von Nissan um den weltweit ersten, in Serie produzierten Motor mit variabler Verdichtung handelt und sein intelligentes Fertigungsprojekt aus Bearbeitungs- und Montagelinie die erste intelligente, automatische Produktionslinie in China ist, die auch das Metallschneiden des Zylinderkopfes und die Motorenmontage umfasst, konnte Comau nicht auf Standarddesignprozesse zurückgreifen.
Um diese Herausforderung zu meistern, wurden während der Design- und Implementierungsphase dank der Innovationen von Comau auf dem Gebiet der Automatisierungstechnologie verschiedene Prozesse für die Produktion eines neuen, energieeffizienten Motors untersucht. Im Prozessdesign wurden auch die hohen Qualitätsanforderungen des Kunden an die Produkte berücksichtigt.
Eine weitere Herausforderung bestand darin, das hohe Produktionsziel des Kunden von 400.000 Einheiten pro Jahr zu erfüllen. Dazu nutzte Comau gleichzeitig sowohl die Effizienzsteigerung durch Industrialisierung als auch die Ressourcen zur Produktion personalisierter Produkte in einem auf intelligente Bearbeitung ausgerichteten Geschäftsmodell – dabei wurden natürlich auch variable Arbeitsbedingungen sowie die Einrichtung von Produktionslinien weltweit berücksichtigt.
Die Lösung
Um die hohen Anforderungen des Kunden an Qualität, Produktion und Effizienz zu erfüllen, entwickelte Comau eine innovative Produktionslinie, die eine Vielzahl fortschrittlicher Automatisierungstechnologien für die Motorenmontage umfasst. Dazu gehört auch der Einsatz von Robotern mit sieben Achsen für die automatische Zylinderkopfladestation, die in der Lage sind, verschiedenste Werkstücke zu ergreifen. Darüber hinaus ermöglicht der Einsatz von Robotern mit sechs Achsen für das automatische Verschrauben die Positionierung in verschiedenen Winkeln im Hinblick auf ein automatisches, flexibles Anziehen. Mit mehr als 60 automatisierten Arbeitsstationen umfasst diese Linie zahlreiche Automatisierungs- und Robotiktechnologien, bei denen Comau mehrere seiner eigenen Lösungen als Teil der Hauptmontageprozesse einsetzen konnte.
Eine solche Innovation ist die von Comau patentierte flexible Fertigungszelle SmartCell. SmartCell fasst automatisierte Montage- und Bearbeitungsprozesse in einer Fertigungszelle zusammen und ist dank der mehrachsigen CNC-Steuerung (Computer Numerical Control) und des schnellen Werkzeugwechsels in der Lage, eine Zylinderkopfmontage in einem Arbeitsgang durchzuführen. Auf diese Weise kann die Motorenmontagelinie eine Vielzahl komplexer Montageprozesse dynamisch bewältigen und bietet aufgrund des hohen Automatisierungsgrades auch die Möglichkeit, Montagearbeiten zu integrieren, die traditionell durch Handarbeit erledigt wurden.
Die flexible Fertigungszelle SmartCell verwendet rechteckige Koordinatenroboter (6-Achsen-Verbindung), mit denen die Montage aller Motorkopfteile, einschließlich Kopfventile, Ventildichtringe, Ventilfedern, Ventilverriegelungsplatten und obere Ventilsitze, vollständig automatisiert werden kann. Durch die Anordnung mehrerer automatischer Schnellwechselvorrichtungen und die parallele Ausführung verschiedener Montageprozesse mit 6-achsigen Robotern wird das vollautomatische Be- und Entladen von Zylinderköpfen und Paletten ausgeführt.
Darüber hinaus ermöglichen eine innovative, flexible Press-Fit-Methode und ein visuelles Positionierungssystem ein automatisches Beladen und ein ungeordnetes Greifen. Comau nutzt das visuelle Positionierungssystem des Roboters, um die Position des Werkstücks im Materialrahmen zu erkennen, das dann nach dem Zufallsprinzip auf dem Zuführtisch für die Serienproduktion ergriffen wird. Auf diese Weise werden eine höhere Produktionsleistung und Flexibilität in Bezug auf die Materialpositionierung vor dem Roboter gewährleistet sowie eine schnellere, präzisere Erkennung von ungeordnet zugeführtem Material. Zukünftig braucht der Kunde bei einem Modell- oder Produktwechsel das Programm einfach nur zu aktualisieren und das System nicht mehr herunterzufahren oder erneut in eine neue Technologie zu investieren. Dadurch werden spätere Wartungskosten eingespart. Noch wichtiger ist jedoch, dass die Ausfallrate der Fertigungslinie auf nahezu Null gesenkt werden kann, was die nachfolgenden Nutzungskosten und die Arbeitsbelastung des Wartungspersonals erheblich reduziert. Ergänzt wird die Fertigungslinie zudem durch die elektrische Zylinderbewegung, den schnellen Wechsel des Indenters und die Bewegung des Werkstücks, durch die das flexible Verpressen jedes beliebigen Teils in jeder Position dynamisch ausgeführt werden kann.
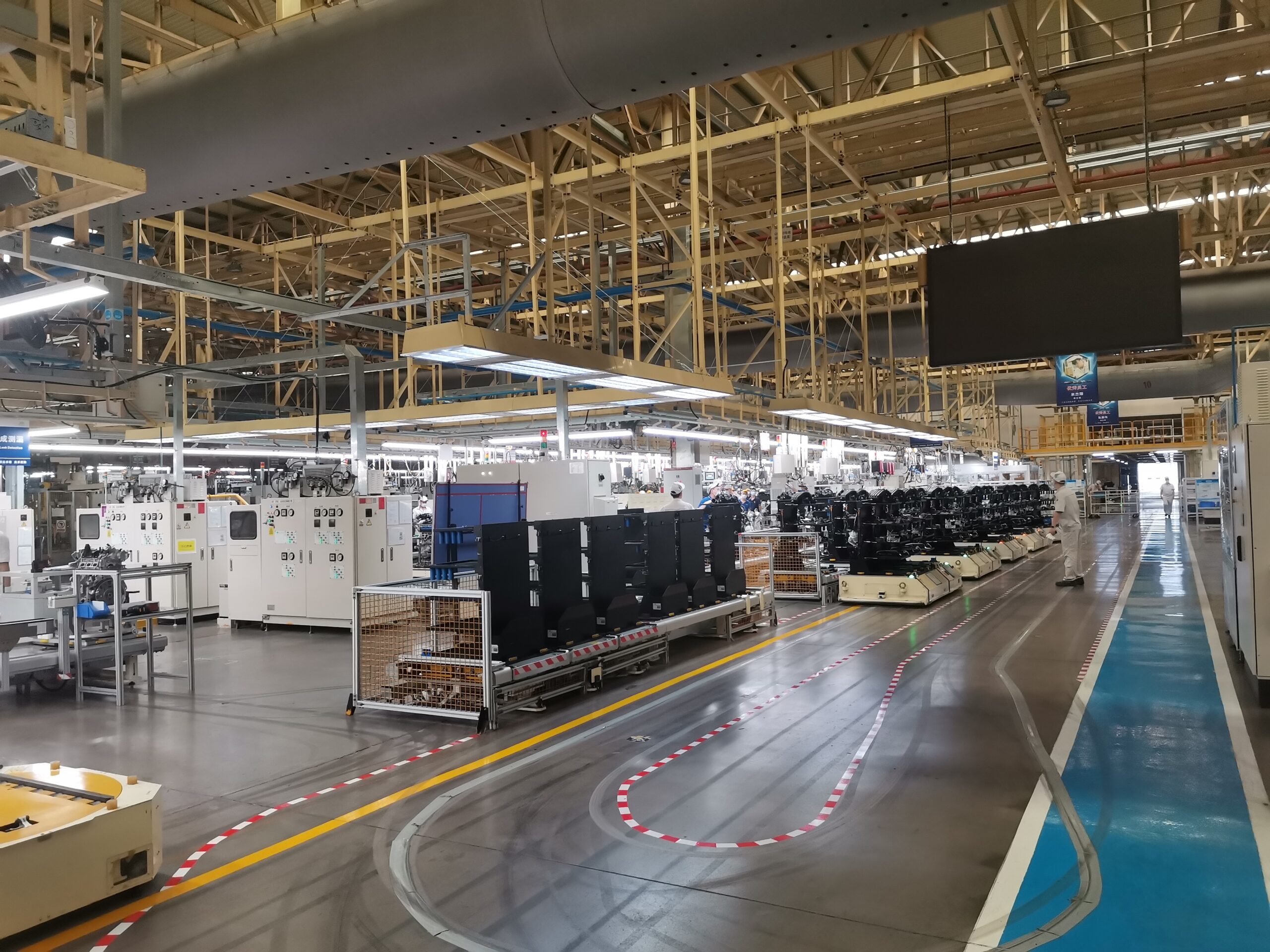
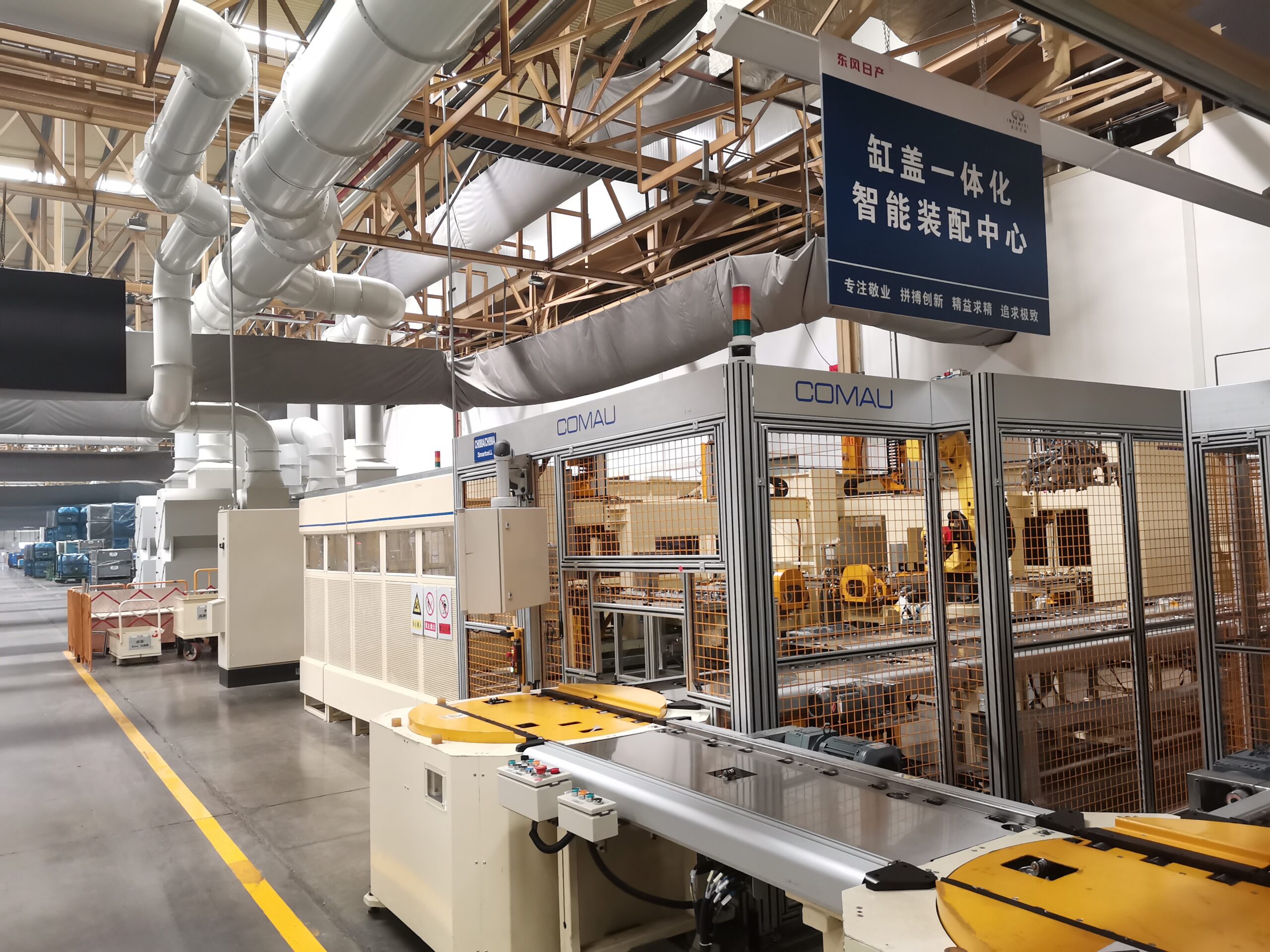
Das Ergebnis
Bei der Umsetzung des Projekts wurde eine Vielzahl fortschrittlicher Technologien eingesetzt, um verschiedene Herausforderungen im Zusammenhang mit der Produktion der neuen energiesparenden Motoren von Nissan zu meistern. Gleichzeitig wurde im Projektdesignprozess die Digitalisierung durch den Einsatz von Software für das Produktlebenszyklusmanagement vom Entwurf bis zur Fertigung genutzt. Die Digitalisierung der gesamten Design-, Produktions- und Fertigungsprozesse bietet Nissan zahlreiche Vorteile wie vollständige Prozesstransparenz, effektive Designqualitätskontrolle, reduzierte Designrisiken, niedrigere Herstellungskosten, verkürzter Produktionszyklus und stellt eine wichtige Datenquelle für die anschließende digitale Fertigung bereit.
Beide Motorenmodelle sind im August 2020 mit einer Jahreskapazität von 400.000 Stück erfolgreich in Serie gegangen. Die Lösung von Comau ermöglicht zudem eine absolut flexible Produktion. Wenn neue oder geänderte Ausrüstungen benötigt werden, müssen nur die Programmierung und die Schnellwechselwerkzeuge angepasst werden, damit der Kunde von einer gemischten Produktion mehrerer Modelle profitieren und gleichzeitig die Automatisierungsrate bei der Motorenherstellung deutlich steigern kann.
„Das Comau-Team hat seine einzigartigen Fähigkeiten bei der vollautomatischen Montage und Bearbeitung unter Beweis gestellt. Das Unternehmen verfügt über die technischen Systeme und die große Erfahrung, die es uns ermöglichen, dieses Projekt sowohl in Bezug auf das Budget als auch auf den Zeitplan wettbewerbsfähig zu halten„,meint Bai Zhongjin, Engine Project Manager von Dongfeng Nissan.
Aufträgen pro Jahr Produktionskapazität
Verschiedenen Motormodellen Effiziente Koproduktion
+
0%
Erfolgsquote bei den Einzelbeladungsmaschinen